Начальный и конечный модули при растяжении
Дата введения 1982-07-01
Постановлением государственного комитета СССР по стандартам от 26 августа 1981 г. N 4058 дата введения установлена 01.07.82
Ограничение срока действия снято по протоколу N 5-94 Межгосударственного совета по стандартизации, метрологии и сертификации (ИУС 11-12-94)
ВЗАМЕН ГОСТ 9550-71
ИЗДАНИЕ (май 2004 г.) с Поправкой (ИУС 11-89).
Настоящий стандарт распространяется на пластмассы и устанавливает методы определения модуля упругости при растяжении, сжатии и изгибе.
Стандарт не распространяется на ячеистые пластмассы и пленки из пластмасс.
Стандарт полностью соответствует СТ СЭВ 2345-80.
Термины, применяемые в настоящем стандарте, и их пояснения приведены в приложении.
1. МЕТОД ОПРЕДЕЛЕНИЯ МОДУЛЯ УПРУГОСТИ ПРИ РАСТЯЖЕНИИ
1.1. Сущность метода
Сущность метода заключается в определении модуля упругости при растяжении как отношения приращения напряжения к соответствующему приращению относительного удлинения, установленному настоящим стандартом.
1.2. Отбор образцов
1.2.1. Для испытания применяют образцы по ГОСТ 11262-80.
1.2.2. Количество образцов, взятых для испытания одной партии материала, а для анизотропных материалов в каждом из выбранных направлений, должно быть не менее 3.
1.3. Аппаратура
Для проведения испытания применяют аппаратуру по ГОСТ 11262-80, при этом испытательная машина должна обеспечивать скорость раздвижения зажимов (1,0±0,5)% в минуту, а прибор для измерения удлинения должен обеспечивать измерение с погрешностью не более 0,002 мм.
1.4. Подготовка к испытанию
1.4.1. Перед испытанием образцы кондиционируют в стандартной атмосфере по ГОСТ 12423-66 не менее 16 ч, если в нормативно-технической документации на конкретную продукцию нет других указаний.
1.4.2. Перед испытанием измеряют толщину и ширину образца по ГОСТ 11262-80.
1.5. Проведение испытания
1.5.1. Испытание проводят при температуре и относительной влажности, указанных в нормативно-технической документации на конкретную продукцию.
Если в нормативно-технической документации на конкретную продукцию нет других указаний, то испытание проводят в соответствии с ГОСТ 12423-66 при температуре (23±2) °С и относительной влажности (50±5)%.
1.5.2. Образец закрепляют в машину так, чтобы продольные оси зажимов и ось образца совпадали с линией, соединяющей точки крепления зажимов на испытательной машине.
1.5.3. На образце, закрепленном в зажимах, проводят установку и настройку прибора для измерения удлинения.
1.5.4. Образец нагружают при скорости раздвижения зажимов испытательной машины, обеспечивающей скорость деформации образца (1,0±0,5)% в минуту. Нагружение осуществляют до величины относительного удлинения 0,5%.
Если образцы разрушаются до достижения относительного удлинения 0,5%, нагружение проводят до меньшей величины деформации, установленной в нормативно-технической документации на конкретную продукцию.
1.5.5. Графическую запись нагрузки и деформации проводят в следующем масштабе:
100-150 мм на диаграмме должно соответствовать 0,4% относительного удлинения;
не менее 100 мм на диаграмме должно соответствовать приращению нагрузки, соответствующему увеличению относительного удлинения на 0,4%.
1.6. Обработка результатов
1.6.1. По диаграмме определяют значения нагрузки, соответствующие величинам относительного удлинения 0,1 и 0,3%. Допускаются меньшие значения относительного удлинения для образцов, предусмотренных в п.1.5.4.
1.6.2. Модуль упругости при растяжении () в МПа вычисляют по формуле
,
где — нагрузка, соответствующая относительному удлинению 0,3%, Н;
— нагрузка, соответствующая относительному удлинению 0,1%, Н;
— расчетная длина образца, мм;
— площадь начального поперечного сечения образца, мм;
— удлинение, соответствующее нагрузке , мм;
— удлинение, соответствующее нагрузке ,
мм.
1.6.3. За результат испытания принимают среднеарифметическое значение всех параллельных определений.
1.6.4. Величину стандартного отклонения вычисляют по ГОСТ 14359-69.
1.6.5. Результаты испытания записывают в протокол, который должен содержать следующие данные:
наименование и марку пластмассы и номер партии;
метод испытания;
наименование испытательной машины;
тип и марку прибора для измерения деформации;
условия проведения испытания (скорость нагружения, температура, графическая запись и т.д.);
тип испытуемого образца (форма, размеры);
условия подготовки испытуемого образца;
количество образцов, взятых для испытания;
среднеарифметическое определяемого показателя и стандартное отклонение;
дату испытания;
обозначение настоящего стандарта.
2. МЕТОД ОПРЕДЕЛЕНИЯ МОДУЛЯ УПРУГОСТИ ПРИ СЖАТИИ
2.1. Сущность метода
Сущность метода заключается в определении модуля упругости при сжатии как отношения приращения напряжения к соответствующему приращению относительной деформации сжатия, установленному настоящим стандартом.
2.2. Отбор образцов
2.2.1. Для испытания применяют образцы по ГОСТ 4651-82. База измерения деформации должна составлять не менее 10 мм и не более высоты образца при измерении деформации прибором, установленным на образце.
При изготовлении образцов из изделий толщиной менее 5 мм используют образцы в форме прямоугольных пластин размерами (80±2)х(10,0±0,5) мм, а толщина образца равна толщине изделия. Для армированных пластмасс ширина образцов равна (15,0±0,5) мм. Для предотвращения потери устойчивости при испытании таких образцов применяют приспособление (черт.1).
Черт.1. Приспособление для испытания на сжатие образцов толщиной менее 5 мм
Приспособление для испытания на сжатие образцов толщиной менее 5 мм
Черт.1
2.2.2. Количество образцов должно соответствовать п.1.2.2.
2.3. Аппаратура
Для проведения испытания применяют аппаратуру по ГОСТ 4651-82, при этом испытательная машина должна обеспечивать скорость сближения опорных площадок со скоростью деформации образца (1,0±0,5)% в минуту, а прибор для измерения деформации сжатия должен обеспечивать измерение с погрешностью не более 0,002 мм.
2.4. Подготовка к испытанию
2.4.1. Перед испытанием образцы кондиционируют в стандартной атмосфере по ГОСТ 12423-66 не менее 16 ч, если в нормативно-технической документации на конфетную продукцию нет других указаний.
2.4.2. Перед испытанием измеряют размеры образцов по ГОСТ 4651-82.
2.5. Проведение испытания
2.5.1. Испытания проводят при температуре и относительной влажности, указанных в п.1.5.1.
2.5.2. Образец устанавливают на опорных плитах испытательной машины так, чтобы продольная ось образца совпадала с направлением действия силы.
2.5.3. Устанавливают прибор для измерения деформации. Деформацию при сжатии определяют измерением расстояния между площадками или по изменению базы на образце (см. п.2.2.1).
2.5.4. Образец нагружают при скорости сближения площадок испытательной машины, обеспечивающей скорость деформации образца (1,0±0,5)% в минуту. Нагружение осуществляют до величины деформации 0,5%.
Если образцы разрушаются до достижения относительной деформации 0,5%, нагружение осуществляют до меньшей величины деформации, установленной в нормативно-технической документации на конкретную продукцию.
2.5.5. Графическую запись нагрузки и деформации проводят в соответствии с п.1.5.5 при значениях относительной деформации сжатия, равных значениям относительного удлинения, указанных в п.1.5.5.
2.6. Обработка результатов
2.6.1. По диаграмме определяют значения нагрузки, соответствующие величинам относительной деформации 0,1 и 0,3%.
Допускаются меньшие значения относительной деформации при сжатии для образцов, предусмотренных в п.2.5.4.
2.6.2. Модуль упругости при сжатии () в МПа вычисляют по формуле
,
где — нагрузка, соответствующая относительной деформации 0,3%, Н;
— нагрузка, соответствующая относительной деформации 0,1%, Н;
— начальная высота образца или базы, мм;
— площадь начального поперечного сечения образца, мм;
— изменение высоты или базы, соответствующее нагрузке , мм;
— изменение высоты или базы, соответствующее нагрузке, ,
мм.
2.6.3. За результат испытания принимают среднеарифметическое значение всех параллельных определений.
2.6.4. Величину стандартного отклонения вычисляют, как указано в п.1.6.4.
2.6.5. Результаты испытания оформляют протоколом, как указано в п.1.6.5.
3. МЕТОД ОПРЕДЕЛЕНИЯ МОДУЛЯ УПРУГОСТИ ПРИ ИЗГИБЕ
3.1. Сущность метода
Сущность метода заключается в определении модуля упругости при изгибе как отношения приращения напряжения к соответствующему приращению относительной деформации, установленному настоящим стандартом.
3.2. Отбор образцов
3.2.1. Для испытания применяют образцы по ГОСТ 4648-71.
3.2.2. Количество образцов должно соответствовать п.1.2.2.
3.3. Аппаратура
Для проведения испытания применяют аппаратуру по ГОСТ 4648-71, при этом испытательная машина должна обеспечивать скорость сближения нагружающего наконечника и опор, соответствующую скорости деформации образца (1,0±0,5)% в минуту, а прибор для измерения деформации образца должен обеспечивать измерение с погрешностью не более 0,01 мм.
3.4. Подготовка к испытанию
3.4.1. Перед испытанием образцы кондиционируют в стандартной атмосфере по ГОСТ 12423-66 не менее 16 ч, если в нормативно-технической документации на конкретную продукцию нет других указаний.
3.4.2. Перед испытанием измеряют размеры образцов по ГОСТ 4648-71.
3.5. Проведение испытания
3.5.1. Испытания на изгиб проводят двумя методами:
А — при нагружении по трехточечной схеме (черт.2);
Б — при нагружении по четырехточечной схеме (черт.3).
Черт.2. Трехточечная схема нагружения при изгибе
Трехточечная схема нагружения при изгибе
Метод А
Черт.2
Черт.3. Четырехточечная схема нагружения при изгибе
Четырехточечная схема нагружения при изгибе
Метод Б
— нагрузка; — расстояние между опорами; — прогиб; — эпюра момента
Черт.3
При методе А испытуемый образец нагружают наконечником в середине расстояния между опорами.
При методе Б испытуемый образец нагружают парой наконечников, расположенных в средней трети расстояния между опорами.
Выбор метода предусматривается в нормативно-технической документации на конкретную продукцию.
Прогиб измеряют:
в методе А — в середине расстояния между опорами (черт.2). Величину прогиба оценивают по величине перемещения подвижной части нагружающего устройства;
в методе Б — в соответствии с черт.3.
3.5.2. Испытания проводят при температуре и относительной влажности, указанных в п.1.5.1.
3.5.3. Расстояние между опорами () устанавливают в зависимости от толщины образца () от 15 до 17 мм и измеряют с погрешностью не более 0,5%.
3.5.4. На образце, лежащем на опорах, осуществляют установку и настройку прибора для измерения прогиба.
3.5.5. Образцы нагружают при скорости сближения нагружающего наконечника и опор, обеспечивающей скорость деформации образца (1,0±0,5)% в минуту.
Нагружение осуществляют до величины относительной деформации крайних волокон 0,5%.
Относительную деформацию крайних волокон () вычисляют по формуле
для метода А
;
для метода Б
,
где — значение прогиба, мм;
— толщина образца, мм;
— расстояние между опорами, мм.
Если образцы разрушаются до достижения относительной деформации крайних волокон 0,5%, нагружение осуществляют до меньшей величины деформации, установленной в нормативно-технической документации на конкретную продукцию.
3.5.6. Графическую запись нагрузки и деформации проводят в соответствии с п.1.5.5 при значениях прогиба, соответствующих значениям относительной деформации крайних волокон, указанных в п.1.5.5.
3.6. Обработка результатов
3.6.1. По диаграмме определяют значения нагрузки и прогиба, соответствующие значениям относительной деформации крайних волокон 0,1 и 0,3%.
Допускаются меньшие значения относительной деформации при изгибе для образцов, предусмотренных в п.3.5.5.
3.6.2. Модуль упругости при изгибе () в МПа вычисляют по формуле
для метода А
;
для метода Б
,
где — расстояние между опорами, мм;
— нагрузка при величине относительной деформации крайних волокон 0,3%, Н;
— нагрузка при величине относительной деформации крайних волокон 0,1%, Н;
— ширина образца, мм;
— толщина образца, мм;
— прогиб образца, соответствующий относительной деформации крайних волокон 0,3%, мм;
— прогиб образца, соответствующий относительной деформации крайних волокон 0,1%, мм
.
3.6.3. За результат испытания принимают среднеарифметическое значение всех параллельных определений.
3.6.4. Величину стандартного отклонения вычисляют, как указано в п.1.6.4.
3.6.5. Результаты испытания оформляют протоколом, как указано в п.1.6.5.
ПРИЛОЖЕНИЕ (справочное). Термины, применяемые в настоящем стандарте, и их пояснения
ПРИЛОЖЕНИЕ
Справочное
Понятие | Обозначение | Единица измерения | Определение |
Модуль упругости | МПа | Мера жесткости материала, характеризующаяся сопротивлением развитию упругих деформаций. | |
при растяжении | МПа | Модуль упругости определяют как отношение приращения напряжения к соответствующему приращению деформации | |
при сжатии | МПа | ||
при изгибе | МПа | ||
2. Скорость деформации | мин | Изменение относительной деформации растяжения или сжатия в единицу времени. Скорость деформации при растяжении и сжатии определяют как отношение скорости перемещения подвижного элемента испытательной машины () к длине образца между кромками зажимов или сжимающими площадками. При изгибе вычисляют по формуле для метода А ; для метода Б , где — скорость относительной деформации крайних волокон образца, равная 0,01 мин; — расстояние между опорами, мм; — толщина образца, мм. |
ПРИЛОЖЕНИЕ. (Поправка).
Текст документа сверен по:
официальное издание
М.: ИПК Издательство стандартов, 2004
Источник
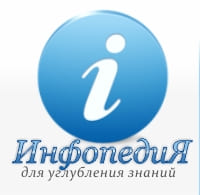
ТОП 10:
Долю реализации вытяжки в процессе монтажа для проводов марки АС можно приближённо оценить по выражению [3]
, (4.1)
где m = 4,28 – отношение сечений алюминиевой части и стального сердечника провода марки АС 240/56 (Табл. 2).
следовательно, примерно 21,4 % длины провода реализуется в процессе монтажа.
Для выполнения расчёта механических характеристик проводов требуется найти следующие модули упругости: C – модуль начального растяжения сталеалюминиевого провода; D – модуль предельной характеристики сталеалюминиевого провода; Cм – монтажный модуль.
Модуль начального растяжения сталеалюминиевого провода [3]
, (4.2)
где Cс = 185 ∙ 103Н / мм2 – модуль начального растяжения стали сердечника провода.
Модуль предельной характеристики сталеалюминиевого провода [3]
, (4.3)
где Dс = 185 ∙ 103Н / мм2 – модуль предельной характеристики стали сердечника провода.
Монтажный модуль определяется через модули начального растяжения и предельной характеристики сталеалюминиевого провода по формуле [3]
(4.4)
Так как оценка механической прочности и монтажных стрел провеса по доле реализации вытяжки провода в монтажном режиме осуществляется для анкерованного участка воздушной линии, то необходимо вычислить значение приведённого пролёта lприв. Из опыта проектирования воздушных линий электропередачи известно, что значение приведённого пролёта lприв составляет
(4.5)
По результатам раздела 2 установлено, что при выборе определяющего механическую прочность провода НСКУ следует ориентироваться на значение критического пролёта lкр2 = 145,28 м. Так как lкр2 < lприв, то определяющим механическую прочность проводов в приведённом пролёте lприв является НСКУ при наибольшей механической нагрузке: γнб, θг, [σ]нб.
Диапазон значений температуры при монтаже провода θм находится в пределах от низшей θ(–) до высшей θ(+) температуры окружающей среды, а именно
Для расчёта зависимости напряжения в низшей точке провода от температуры при монтаже σм = f (θм) в приведённом пролёте, составим и решим уравнение состояния провода, в котором исходными являются условия, определяющие механическую прочность проводов: γнб, θг, [σ]нб, а искомыми – монтажные условия: γ1, θм, σм
(4.6)
Найдём коэффициенты Aм, Bм неполного кубического уравнения состояния провода
(4.7)
(4.8)
Решение уравнения (4.6) находим с помощью метода Ньютона по формуле (2.5) для всех значений температур при монтаже θм, задаваемых из диапазона θ(–) ≤ θм ≤ θ(+).
Далее находим начальное приближение напряжения в низшей точке провода при монтаже σм,0 по эмпирическим формулам согласно [3]
— если Aм < 0, то
(4.9)
— если Aм > 0, то
(4.10)
Например, температура при монтаже равна θм = – 42 оС, тогда по формуле (4.7)
Так как коэффициент Aм < 0, то воспользуемся выражением (4.9) для нахождения σм,0
Итерационный процесс методом Ньютона выполняем при достижении заданной точности расчёта ξ = 0,1 Н / мм2
, ,
, ,
таким образом, на второй итерации i = 2 требуемая точность расчёта σм достигнута.
Дальнейший расчёт σм для других значений θм аналогичен, поэтому результаты сведём в Табл. 4.1. По данным Табл. 4.1 построим график зависимости σм = f (θм) (Рис. 4.1).
Табл. 4.1 – Результаты расчёта напряжения в низшей точке проводов в зависимости от температуры при монтаже
θм, оС | Aм, Н / мм2 | σм,0, Н / мм2 | σм,1, Н / мм2 | σм,2, Н / мм2 |
– 42 | -55,575 | 60,47 | 62,02 | 61,98 |
– 37 | -62,414 | 58,97 | 60,63 | 60,6 |
– 32 | -69,254 | 57,57 | 59,32 | 59,28 |
– 27 | -76,093 | 56,27 | 58,07 | 58,03 |
– 22 | -82,932 | 55,05 | 56,89 | 56,85 |
– 17 | -89,772 | 53,91 | 55,76 | 55,72 |
– 12 | -96,611 | 52,83 | 54,69 | 54,65 |
– 7 | -103,45 | 51,82 | 53,67 | 53,62 |
-113,03 | 50,5 | 52,32 | 52,27 | |
+ 3 | -117,129 | 49,96 | 51,76 | 51,72 |
+ 8 | -123,969 | 49,1 | 50,87 | 50,83 |
+ 13 | -130,808 | 48,28 | 50,02 | 49,98 |
+ 18 | -137,647 | 47,51 | 49,21 | 49,17 |
+ 23 | -144,487 | 46,77 | 48,43 | 48,39 |
+ 28 | -151,326 | 46,06 | 47,68 | 47,64 |
+ 33 | -158,165 | 45,39 | 46,96 | 46,93 |
Рассчитаем стрелы провеса проводов f следующих длин характерных пролётов трассы воздушной линии: lприв – приведённого пролёта, lгаб – габаритного пролёта, lmax – максимального пролёта.
Приближённое значение максимального пролёта lmax найдём из соотношения [3]
(4.11)
Рис. 4.1 – Зависимость напряжения в низшей точке провода от температуры при монтаже |
Далее для характерных пролётов трассы воздушной линии рассчитаем стрелы провеса в них в зависимости от температуры при монтаже θм.
Стрела провеса приведённого пролёта lприв в процессе монтажа равна [3]
(4.12)
Стрелу провеса в габаритном пролёте lгаб выразим через стрелу провеса в приведённом пролёте lприв
(4.13)
Стрелу провеса в максимальном пролёте lmax также выразим через стрелу провеса в приведённом пролёте lприв, получим
(4.14)
Так, например, при θм = – 42 оС, σм = 61,98 Н / мм2 получим
Расчёт при других значениях температуры при монтаже θм (Табл. 4.1) аналогичен, результаты сведём в монтажную таблицу (табл. 4.2).
Табл. 4.2 – Монтажная таблица значений стрел провеса проводов для характерных длин пролёта трассы воздушной линии в зависимости от температуры при монтаже
θм, оС | σм, Н / мм2 | Значения стрел провеса проводов для характерной длины пролёта, м | ||
lприв = 330 м | Lгаб = 366,65 м | lmax = 458,31 м | ||
– 42 | 61,98 | 8,02 | 9,89 | 15,46 |
– 37 | 60,6 | 8,2 | 10,12 | 15,81 |
– 32 | 59,28 | 8,38 | 10,34 | 16,16 |
– 27 | 58,03 | 8,56 | 10,57 | 16,51 |
– 22 | 56,85 | 8,74 | 10,79 | 16,86 |
– 17 | 55,72 | 8,92 | 11,01 | 17,2 |
– 12 | 54,65 | 9,09 | 11,22 | 17,53 |
– 7 | 53,62 | 9,26 | 11,44 | 17,87 |
52,27 | 9,5 | 11,73 | 18,33 | |
+ 3 | 51,72 | 9,6 | 11,86 | 18,53 |
+ 8 | 50,83 | 9,77 | 12,06 | 18,85 |
+ 13 | 49,98 | 9,94 | 12,27 | 19,17 |
+ 18 | 49,17 | 10,1 | 12,47 | 19,49 |
+ 23 | 48,39 | 10,26 | 12,67 | 19,8 |
+ 28 | 47,64 | 10,43 | 12,87 | 20,11 |
+ 33 | 46,93 | 10,58 | 13,07 | 20,42 |
Монтажные графики, построенные по данным Табл. 4.2, представлены на Рис. 4.2.
Рис. 4.2 – Монтажные графики зависимости стрел провеса в характерных пролётах трассы воздушной линии от температуре при монтаже |
ВЫВОДЫ ПО РАЗДЕЛУ 4
В результате выполнения раздела 4: определена доля реализации вытяжки ν провода марки АС 250/56 в процессе монтажа – ν ≈ 0,214; рассчитано значение монтажного модуля – Cм = 7,475 ∙ 104Н / мм2, соответствующего значению доли реализации вытяжки провода ν; выполнена оценка механического напряжения в низшей точке провода для приведённой длины пролёта lприв трассы воздушной линии в зависимости от температуры при монтаже σм = f (θм) (Рис. 4.1); построены графики зависимости стрел провеса fприв , fгаб , fmax для характерных длин пролёта трассы воздушной линии в зависимости от температуры при монтаже θм (Рис. 4.2).
Источник