Допускаемое напряжение растяжения шпильки
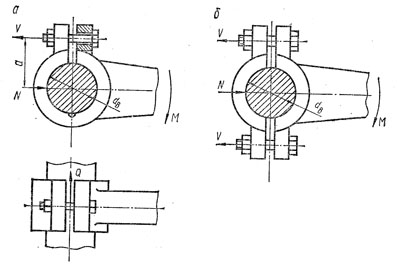
Приложение Г
(обязательное)
Допускаемые напряжения для материала болтов (шпилек)
Номинальное допускаемое напряжение для болтов (шпилек) при затяжке и испытании вычисляют по формуле (Г.1) при температуре 20 °С.
Номинальное допускаемое напряжение для болтов (шпилек) в рабочих условиях вычисляют по формулам (Г.1), (Г.2), но не более номинального допускаемого напряжения при затяжке:
— если расчетная температура для болтов (шпилек) из углеродистых сталей не превышает 380 °С, низколегированных сталей — 420 °С, аустенитных сталей — 525 °С:
;
(Г.1)
— если расчетная температура болтов (шпилек) из углеродистых сталей превышает 380 °С, низколегированных сталей — 420 °С, аустенитных сталей — 525 °С:
;
(Г.2)
где nТ — коэффициент запаса по отношению к пределу текучести:
nТ = 2,6 — 2,8 — для углеродистых сталей, у которых / 0,7;
nТ = 2,3 — для углеродистых сталей, у которых / < 0,7;
nТ = 1,9 — для сталей аустенитного класса;
nD = 1,8 — коэффициент запаса прочности по пределу длительной прочности;
nп = 1,1 — коэффициент запаса прочности по пределу ползучести.
Допускаемые напряжения для болтов (шпилек) при затяжке в рабочих условиях и при расчете на условия испытания вычисляют по формулам:
;
(Г.3)
,
(Г.4)
где = 1,2 — коэффициент увеличения допускаемых напряжений при затяжке;
Kу.р — коэффициент условий работы:
Kу.р = 1,0 — для рабочих условий;
Kу.р = 1,35 — для условий испытания;
Kу.з — коэффициент условий затяжки:
Kу.з = 1,0 — при обычной не контролируемой затяжке;
Kу.з = 1,1 — при затяжке с контролем по крутящему моменту (см. приложение Л);
Kу.з = 1,3 — при затяжке с помощью одновременной контролируемой вытяжке шпилек.
Рекомендуемые значения крутящих моментов при затяжке приведены в приложении Л;
Kу.т — коэффициент учета нагрузки от температурных деформаций:
Kу.т = 1,0 — если нагрузка от температурных деформаций не учитывается;
Kу.т = 1,3 — при расчете фланцев с учетом нагрузки от температурных деформаций.
Номинальные допускаемые напряжения для болтов (шпилек) приведены в таблице Г.1.
Таблица Г.1 — Номинальные допускаемые напряжения для болтов (шпилек)
Расчетная температура болтов (шпилек), °С | Номинальное допускаемое напряжение для болтов (шпилек), МПа | |||||||
Марки материала | ||||||||
35, 40 | 12Х18Н10Т, 10Х17Н13М2Т | 45X14H14B2M | 20X13 | 35X, 40X, 38XA, 37Х12Н8Г8МБФ, 20XH3A | 30ХМА | 25X1МФ | Алюминиевый сплав Д16 | |
20 | 130,0 | 110,0 | 160,0 | 195,0 | 230,0 | 230,0 | 238,0 | 83 |
100 | 126,0 | 105,0 | 150,0 | 182,0 | 230,0 | 230,0 | 227,0 | 80 |
200 | 120,0 | 98,0 | 150,0 | 165,0 | 225,0 | 200,0 | 217,0 | 76 |
250 | 107,0 | 95,0 | 144,0 | 158,0 | 222,0 | 182,0 | 210,0 | — |
300 | 97,0 | 90,0 | 139,0 | 150,0 | 222,0 | 174,0 | 199,0 | — |
350 | 86,0 | 86,0 | 128,0 | 147,0 | 185,0 | 166,0 | 185,0 | — |
375 | 80,0 | 85,0 | 128,0 | 146,0 | 175,0 | 166,0 | 180,0 | — |
400 | 75,0 | 83,0 | 128,0 | 145,0 | 160,0 | 166,0 | 175,0 | — |
425 | 68,0 | 82,0 | 125,0 | 143,0 | 156,0 | 161,0 | 168,0 | — |
450 | — | 80,0 | 123,0 | 142,0 | — | 156,0 | 161,0 | — |
475 | — | 79,0 | 120,0 | 140,0 | — | — | 132,0 | — |
500 | — | 78,0 | 118,0 | — | — | — | 73,0 | — |
510 | — | 75,0 | 117,0 | — | — | — | 62,0 | — |
520 | — | 73,0 | 116,0 | — | — | — | — | — |
530 | — | 70,0 | 115,0 | — | — | — | — | — |
540 | — | 65,0 | 114,0 | — | — | — | — | — |
550 | — | 63,0 | 113,0 | — | — | — | — | — |
600 | — | 56,0 | — | — | — | — | — | — |
20 | 238,0 | 238,0 | 238,0 | 232,0 | 321,0 | 191,0 | 208,0 | 231,0 |
100 | 232,0 | 234,0 | 234,0 | 230,0 | 314,0 | 145,5 | 196,0 | 226,0 |
200 | 231,0 | 224,0 | 231,0 | 220,0 | 312,5 | 144,5 | 186,0 | 221,0 |
250 | 224,0 | 213,0 | 227,0 | 218,0 | 309,5 | 131,0 | 186,0 | 219,0 |
300 | 220,0 | 202,0 | 227,0 | 209,0 | 307,0 | 118,0 | 186,0 | 217,0 |
350 | 213,0 | 185,0 | 220,0 | 207,0 | 307,0 | 115,5 | 186,0 | 215,0 |
375 | 209,0 | 183,0 | 216,0 | — | — | 114,0 | 186,0 | 214,0 |
400 | 206,0 | 182,0 | 213,0 | — | — | 113,0 | 186,0 | 213,0 |
425 | 202,0 | 178,0 | 208,0 | — | — | — | 186,0 | 213,0 |
450 | 199,0 | 175,0 | 203,0 | — | — | — | 186,0 | 213,0 |
475 | 195,0 | 171,0 | 196,0 | — | — | — | 186,0 | 213,0 |
500 | 139,0 | 145,0 | 172,0 | — | — | — | 186,0 | 208,0 |
510 | 128,0 | 138,0 | 164,0 | — | — | — | 185,0 | 205,0 |
520 | 117,0 | 131,0 | 156,0 | — | — | — | 184,0 | 202,0 |
530 | 107,0 | 124,0 | 147,0 | — | — | — | 183,0 | 199,0 |
540 | 64,0 | 117,0 | 139,0 | — | — | — | 181,0 | 196,0 |
550 | — | 110,0 | 131,0 | — | — | — | 180,0 | 195,0 |
560 | — | 103,0 | 122,0 | — | — | — | 165,0 | 183,0 |
570 | — | — | — | — | — | — | 150,0 | 171,0 |
580 | — | — | — | — | — | — | 135,0 | 169,0 |
590 | — | — | — | — | — | — | 120,0 | 157,0 |
600 | — | — | — | — | — | — | 115,0 | 147,0 |
610 | — | — | — | — | — | — | 110,0 | — |
620 | — | — | — | — | — | — | 105,0 | — |
630 | — | — | — | — | — | — | 100,0 | — |
640 | — | — | — | — | — | — | 94,0 | — |
650 | — | — | — | — | — | — | 88,0 | — |
Источник
Расчет на прочность резьбового соединения обычно производят по одному критерию −прочности нарезанной части. При этом внутренний диаметр резьбы принимают равным
d1 = d – 0.94p (10.8)
где d — наружный (номинальный) диаметр резьбы.
Таблица 10.1– Параметры резьбы
Номинальный диаметр резьбы, d | Резьба с крупным шагом | Резьба с мелким шагом | |
шаг резьбы р | средн. диаметр d2 | шаг резьбы р | средн. диаметр d2 |
1,5 | 9,02 | 1,25 | 9,18 |
1,75 | 10,86 | 1,25 | 11,18 |
14,7 | 1,5 | 15,02 | |
2,5 | 18,37 | 1,5 | 19,02 |
22,05 | 22,7 |
Определив по формуле (7) и (8) внутренний и средний диаметр резьбы, по таблице 10.1 находим размер резьбы болта и ее шаг. Например, вычисленному среднему диаметру болта d2 = 14,7 мм соответствует болт с номинальным диаметром резьбы 16 мм и крупным шагом 2 мм т.е. М16 х 2.
Основные случаи расчетов резьбовых соединений
Существует 6 случаев расчета резьбовых соединений, рассмотрим первые два из них.
Случай
Болт нагружен только внешней растягивающей силой (грузовой крюк подъемного крана). Гайка свободно навинчивается на стержень и фиксируется шплинтом (рисунок 10.7).
Рисунок 10.7 – Грузовой крюк
Внутренний диаметр d1 резьбы болта, определяется из условия прочности на растяжение
, (10.9)
откуда , (10.10)
где F – растягивающая сила,
σТ допускаемое напряжение,
σТ — предел текучести (по таблице).
По значению d1 из таблицы выбирают шаг и резьбу.
Случай
Болт затянут силой F0, внешняя нагрузка отсутствует – болты для крепления крышек корпусов механизма. Здесь болт испытывает растяжение и кручение. Эти силы заменяют одной Fрасч
Fрасч=1,3F0, (10.11)
, (10.12)
откуда , (10.13)
где , (10.14)
σТ− предел текучести материала болта,
− коэффициент запаса прочности (по таблице).
В начале расчета ориентировочно задают диаметр резьбы и по таблице принимают . Если после расчета получается диаметр, который не лежит в принятом интервале, задаются другим диаметром и расчет повторяют. Для грузовых соединений диаметр болта принимают равным не менее 8 мм.
Класс прочности и материалы резьбовых деталей
Стальные винты, болты и шпильки изготавливают 12 классов прочности, которые обозначают двумя числами 3.6, 4.6, 4.8, 5.6, 5.8, 6.6…14.9.
Первое число умноженное на 100 указывает минимальное значение предела прочности σв в МПа, а произведение чисел умноженные на 10 – значение предела текучести σТ (для класса 3.6 приблизительно 200, а для класса 4,6: 4 х 6 х 10 = 240) и т. д.
Таблица 10.2–Класс и пределы прочности резьбовых деталей
Класс прочности | Предел прочности σв МПа | Предел текучести σT МПа | Марка стали |
min | max | болта | гайки |
3,6 | 340. 300 | Ст 3; 10 | Ст 3 |
4,6 | Ст 3 | ||
5,6 | 30; 35 | ||
6,6 | 35; 45; 401 |
Пример:
Определить диаметр резьбы болта скобы грузового крана по условию прочности, если F=17 кН класс прочности 5.6.
1. По таблице находим σТ=5· 6 ·10 = 300 МПа
σp= 0,6 ·300 = 180 МПа
2. Внутренний диаметр резьбы болта
Определяем наружный и средний диаметр резьбы
d= d1/ 0,8 = 10,96/0,8 = 13,70 мм
d2 = (d1 + d)/2 = (10,96 + 13,70)/2 = 12,33 мм
По таблице 3.1 принимаем номинальный диаметр резьбы больше чем 12 мм, т.е. d = 16 мм с шагом 2 мм. Тогда болт будет иметь обозначение М16х2.
Стандартные крепежные резьбовые детали общего назначения изготавливают из низко и среднеуглеродистых сталей Ст3; 10; 20; 35.
Легированные стали – 35х30хГСА применяются для ответственных винтов, болтов, гаек и шпилек.
Для защиты от коррозии детали оксидируют, омедняют, оцинковывают, хромируют и т. д.
Кроме стали, могут применяться неметаллические материалы (нейлоны, полиамиды и др.).
Источник
Болт поставлен без зазора в отверстие из-под развертки
Силы, перпендикулярные к оси болта, вызывают срез. Условие прочности болта
где τср — расчетное напряжение на срез, Н/мм2;
τср — (0,2 — 0,3)σt —допускаемое напряжение на срез;
σt — предел текучести материала болта, Н/мм2
Q — сила, действующая на соединение, Н;
i — число плоскостей среза (на рисунке i = 1);
d б — диаметр ненарезанной части болта, мм.
Поверхности контакта соединяемых деталей и ненарезанной части болта проверяют на смятие:
σсм — расчетное напряжение смятия, Н/мм2;
δ min — наименьшая толщина соединяемых деталей, находящихся в контакте с болтом мм;
[σ] см — допускаемое напряжение смятия, Н/мм2:
для стали углеродистой [σ] см — (0,8 — 1,0)σ т ;
для стали легированной [σ] см — (0,6 — 0,8)σ т
для чугуна [σ] см — (0,6 — 0,8)σ пчр
Расчет прецизионных (призонных) болтов, которые вставляют в конические отверстия
Болт, поставленный с зазором, воспринимает нагрузку, перпендикулярную к оси
Силу, с которой нужно затянуть болт — ее называют силой затяжки и определяют из условия, — чтобы не было сдвига деталей, т. е. чтобы сила трения Т на стыках соединяемых деталей была не меньше сдвигающей силы, обычно принимают с учетом запаса против сдвига деталей T = 1,2Q.
Для болта в данном соединении требуемая сила затяжки
где Q — сдвигающая сила;
i — число стыков ( i = 1);
f — коэффициент трения для стыка.
Для сухих обработанных стыков стальных или чугунных деталей
f = 0,10…0,15; то же при наличии масляной пленки f = 0,06.
В стыках стальных конструкций:
при пескоструйной обработке стыка f = 0,5;
при обработке пламенем газовой горелки f = 0,4;
при необработанных стыках (со следами окалины) f = 0,3;
при окраске алюминиевым порошком f = 015;
при окраске антикоррозионной краской f = 0,10;
при окраске свинцовым суриком f = 0,06
По найденной силе затяжки V рассчитывают болт на совместное действие растяжения и кручения. На практике влияние кручения для стандартных метрических резьб учитывают приближенно, вводя коэффициент 1,3. Тогда условие прочности
где F1 = πd21/4 — площадь поперечного сечения по внутреннему диаметру резьбы, мм2;
[σ]p = σ т/ [n] — допускаемое напряжение, Н/мм2
σ т — предел текучести материала болта, Н/мм2;
[n] — требуемый коэффициент запаса:
при контролируемой затяжке для болтов из углеродистой стали [n] = 1,6; для болтов из легированной стали [n] = 2
при неконтролируемой затяжке коэффициенты запаса [n] принимают в зависимости от диаметра резьбы:
Значения [n] при номинальном диаметре резьбы d, мм
Материал болтов | Ø 6 — 16 | Ø 16 — 30 | Ø 30 — 60 |
Углеродистая сталь | 5 — 4 | 4 — 2,5 | 2,5 — 1,7 |
Легированная сталь | 6,5 — 5 | 5 — 3,3 | 3,3 — 3 |
На практике чаще приходится иметь дело с неконтролируемой затяжкой. Поэтому для затянутых болтов с резьбой от М6 до М48 при неконтролируемой затяжке подсчитаны допускаемые осевые нагрузки [Р], которые приведены в таблице
Допускаемые осевые нагрузки [P] в кН для затянутых болтов при неконтролируемой затяжке
Материал | Ст 3 | Сталь 35 | Сталь 45 | 12ХН2 | 40Х |
---|---|---|---|---|---|
σ т, Н/мм2 | 210 | 320 | 360 | 600 | 800 |
М6 | 0,80 | 1,20 | 1,35 | 1,75 | 2,30 |
М8 | 1,45 | 2,20 | 2,50 | 3,20 | 4,20 |
М10 | 2,55 | 3,90 | 4,40 | 5,50 | 7,30 |
М12 | 3,70 | 5,70 | 6,40 | 8,00 | 10,50 |
(М14) | 5,75 | 8,80 | 9,90 | 13,00 | 17,50 |
М16 | 7,90 | 12,00 | 13,50 | 18,00 | 24,00 |
(М18) | 9,60 | 14,50 | 16,50 | 22,00 | 29,50 |
М20 | 14,00 | 21,50 | 24,00 | 31,00 | 41,00 |
(М22) | 20,00 | 31,00 | 35,00 | 43,00 | 58,00 |
М24 | 23,50 | 36,00 | 40,00 | 50,00 | 67,00 |
(М27) | 37,00 | 56,00 | 63,00 | 80,00 | 105,00 |
М30 | 45,00 | 69,00 | 77,00 | 98,00 | 130,00 |
М36 | 73,00 | 110,00 | 125,00 | 145,00 | 195,00 |
М42 | 100,00 | 150,00 | 170,00 | 200,00 | 270,00 |
М48 | 130,00 | 235,00 | 255,00 | 275,00 | 365,00 |
Примечание. Размеры болтов, заключенные а скобки, применять не рекомендуется
Уточненный расчет
При более точных расчетах определяют эквивалентное напряжение
где, напряжение растяжения в поперечном сечении нарезанной части болта
наибольшее напряжение кручения в поперечном сечении нарезанной части болта
момент в резьбе
d2 — средний диаметр резьбы;
λ — угол подъема резьбы;
ρ ‘ — приведенный угол трения, определяемый из соотношения
f — коэффициент трения
условный коэффициент трения между витками резьбы с углом профиля а или иначе приведенный коэффициент трения.
Условие прочности
Болты клеммового (фрикционно — винтового) соединения
а — клемма с разрезной ступицей; б — клемма с разъемной ступицей
Эти болты также ставятся с зазором. Их затягивают так, чтобы момент трения М тр на стыке вала и клеммы был не меньше вращающего момента М; обычно принимают с учетом запаса сцепления М тр=1,2М
В общем случае клеммы могут быть нагружены одновременно осевой силой Q и вращающим моментом М. Клемма с разрезной ступицей менее удобна, чем клемма с разъемной ступицей. Последнюю можно устанавливать в любой части вала, не трогая насаженных на вал деталей.
Требуемая сила затяжки болтов клеммовых соединений зависит от принятого закона распределения давлений на поверхности контакта ступицы клеммы и вала. Наиболее неблагоприятной является посадка клеммы с большим зазором, когда контакт полуступиц с валом происходит по линиям; при затяжке болтов линейный контакт переходит в контакт по узкой площадке. При небольших зазорах, что соответствует в незатянутом состоянии посадкам h6 или g6, после затяжки закон распределения давлений оказывается близким к косинусоидальному. Наличие натяга в незатянутом соединении, что соответствует посадкам r6 или n6, обеспечивает после затяжки примерно равномерное распределение давлений
Рассматривается общий случай действия осевой силы Q и вращающего момента М. Расчет ведут либо по равнодействующей осевой и окружной сил, приведенной к поверхности контакта
либо отдельно по моменту М, стремящемуся повернуть клемму, и по силе Q, стремящейся сдвинуть клемму по валу.
Необходимая сила V затяжки болта
Винт нагружен осевой силой Q; возможно подтягивание под нагрузкой
Винты стяжных устройств работают на растяжение от внешних сил Q и на кручение от момента в резьбе М р
Расчет на прочность проводят по формуле
с заменой V на Q.
Болт с внецентренной растягивающей нагрузкой
При затяжке такой болт, имеющий эксцентричную или костыльную головку, испытывает растяжение, изгиб и кручение
Наибольшее суммарное нормальное напряжение
При значительных эксцентриситетах (е >0,1d) влияние кручения мало и его не учитывают. Тогда условие прочности
При малых эксцентриситетах (е <0,1d) расчет выполняют на совместное действие растяжения, изгиба и кручения
где
Изгиб болта (шпильки) может вызываться не только эксцентричностью нагружения, обусловленного формой головки болта, но и возникать из-за перекоса опорных поверхностей. Так, при перекосе торца гайки напряжения изгиба в поперечном сечении стержня шпильки
где Θ = Ml/EJ — угол перекоса в радианах;
Е — модуль продольной упругости материала шпильки;
d ст — диаметр стержня шпильки;
l — длина шпильки
Напряжения изгиба в поперечном сечении нарезанной части шпильки
Из формулы следует, что для уменьшения напряжений σ и‘ необходимо изготовлять шпильку с возможно меньшим диаметром стержня d cт
Затянутый болт дополнительно нагружается осевой нагрузкой
Крепление крышек двигателей внутреннего сгорания, автоклавов и сосудов, находящихся под внутренним давлением.
Болты такого соединения должны быть при монтаже затянуты так сильно, чтобы гарантировать герметичность после приложения осевой нагрузки.
При соединении стальных или чугунных деталей ориентировочный расчет болта можно проводить на растяжение силой
Р = 1,3Q
где Р — осевая сила, действующая на болт, от предварительной затяжки;
Q — внешняя осевая сила
Источник
Допускаемые напряжения для расчета резьбовых соединений — Мегаобучалка
Допускаемые напряжения растяжения для винтов, болтов и шпилек определяют по зависимости [1, с.73]: [ σ Р ] = σТ / [ s ]Т , (20) где σТ – предел текучести материала, из которого изготовлен болт, МПа; [ s ]Т – коэффициент запаса прочности материала при расчете болтов в соединениях с неконтролируемой затяжкой (табл. 4). Таблица 4 – Значения коэффициента запаса прочности [ s ]Т для расчета болтов в соединениях с неконтролируемой затяжкой [1, с.73]
При контролируемой затяжке соединения значение допускаемого коэффициента запаса прочности [s] не зависит от параметров резьбы: [ S ]= 1,7…2,2 для углеродистых сталей; [ S s ] = 2 … 3 для легированных сталей. Допускаемые напряжения среза для стандартных винтов (болтов) рекомендуется принимать: [ t СР ]= (0.2 …0.3) s Т [1, с.75]. Допускаемые напряжения смятия [3, с. 89]: при соединении стальных деталей [ s СМ ] = 0,8 s Т ; при соединении чугунных деталей [ s СМ ] = (0,4…0,5) s В . Выбор исходных данных к проектированию соединений Исходные данные для проектирования неразъемного соединения следует выбирать в соответствии с номером задачи и вариантом по Приложению 1. Исходные данные для проектирования разъемного соединения следует выбирать в соответствии с номером задачи и вариантом по Приложению 2. Основная литература 1. Куклин Н.Г. Детали машин. Учебник. / Н.Г. Куклин, Г.С. Куклина, В.К. Житков. – М.: Высш. школа, 2005. – 396 с. 2. ГОСТ 2.315-68 Единая система конструкторской документации. Изображения упрощенные и условные крепежных деталей. М.: Издательство стандартов, 2009. – 11с. Дополнительная литература 3. Дмитриев В.Г., Иванов С.Д., Гузенков П.Г. Детали машин. Учебник. – М.: МГОУ, 2001. – 304 с. 4. Орлов П.И. основы конструирования: В 2 Кн. Кн. 2. – М.: Машиностроение, 1988. – 544с.: ил. 5. Теория механизмов и машин и детали машин. Методические указания и задания на контрольные и курсовую работы. / Гузенкова М.П., Серебренников В.И., Симонян А.А. – М.: Высш. шк. , 1983. – 78 с., ил. Приложение 1 Задача 1 [5, с. 40]. Проверить прочность сварных швов зубчатого колеса, соединяющих диск с ободом и со ступицей (рис. 1.1). Материал диска – сталь Ст. З, а ступицы и обода – сталь 35. Передаваемая валом мощность Рпри угловой скорости ω, размеры катетов сварных швов: k 1 = 8 мм, k 2= 10 мм. Нагрузка статическая. Сварка ручная электродом Э42. Рисунок 1.1 – Сварное зубчатое колесо Таблица 1.1– исходные данные к расчетам [5, с. 40]
Приложение 1 Задача 2 [5, с. 41]. Рассчитать сварное соединение растяжки с косынкой, приваренной к плите (рис. 2). Подобрать сечение растяжки, выполненной из уголков. α – угол наклона растяжки. F – усилие, приложенное к уголкам. Нагрузка статическая. δ – толщина косынки; δ = 10 мм. Сварка ручная. Рисунок 1.2 – Сварное соединение растяжек с косынкой Таблица 1.2 – исходные данные к расчетам
Приложение 1 Задача 3 [5, с. 41]. Рассчитать клепаную конструкцию (рис. 1.3), состоящую из косынки и двух уголков.Определись номер профиля уголков и число заклёпок. F – сила, приложенная к уголкам. Нагрузка статическая. Материал косынки и заклёпок — сталь Ст. З. Рисунок 1.3 – Клепаное соединение двух уголков с косынкой Таблица 1.3 – исходные данные к расчетам Параметры | Варианты исходных данных | |||||||||||||||||||||||||||||||||||||||||||||||||||||||||||||||||||||||||||||||||||||||||||||||||||||||||||||||||||||||||||||||||||||||||||||||
1 | 2 | 3 | 4 | 5 | 6 | 7 | 8 | 9 | 10 | |||||||||||||||||||||||||||||||||||||||||||||||||||||||||||||||||||||||||||||||||||||||||||||||||||||||||||||||||||||||||||||||||||||||
F, кН | 35 | 40 | 45 | 50 | 55 | 60 | 65 | 70 | 75 | 80 | ||||||||||||||||||||||||||||||||||||||||||||||||||||||||||||||||||||||||||||||||||||||||||||||||||||||||||||||||||||||||||||||||||||||
δ, мм | 10 | 10 | 10 | 12 | 12 | 12 | 12 | 15 | 15 | 15 |
Приложение 1
Задача 4 [ 5, с. 42].
Определить допускаемую силу [ F ], которая может быть приложена, исходя из прочности, сварных швов, на конце клеммового рычага (рис. 4.1).
а – размер рычага у места сварки.
к – размер катета шва.
Материал рычага – сталь Ст. З.
Сварка ручная.
Рисунок 1.4 – Сварной клеммовый рычаг
Таблица1.4– исходные данные к расчетам
Параметры | Варианты исходных данных | |||||||||
1 | 2 | 3 | 4 | 5 | 6 | 7 | 8 | 9 | 10 | |
а, мм | 35 | 45 | 55 | 60 | 70 | 80 | 90 | 90 | 100 | 110 |
L , мм | 0,65 | 0,70 | 0,75 | 0,80 | 0,85 | 0,80 | 0,90 | 0,95 | 1,0 | 0,95 |
k , мм | 5 | 6 | 7 | 8 | 10 |
Приложение 1
Задача 5 [5, с. 42].
Рассчитать сварное соединение стойки ручной лебёдки с плитой.
F – сила натяжения каната. Нагрузка статическая.
α –угол наклона силы F (см. рис. 5.1).
δ – толщина стойки; δ=12 мм.
L – расстояние между стойками; L = 600мм.
Н – высота оси барабана.
а – крайнее положение каната на барабане относительно стойки;
а =100 мм.
Материал плиты и стойки – сталь Ст. 3. Сварка ручная.
Рисунок 1.5 – Сварная рама для барабана лебедки
Таблица 1.5 – исходные данные к расчетам
Параметры | Варианты исходных данных | |||||||||
1 | 2 | 3 | 4 | 5 | 6 | 7 | 8 | 9 | 10 | |
F , кН | 36 | 26 | 37 | 27 | 48 | 28 | 39 | 49 | 25 | 50 |
Н, мм | 700 | 600 | 500 | 700 | 600 | 500 | 700 | 600 | 500 | 700 |
α, рад. | π/4 | π/6 | π/9 | π/12 | π/9 | π/4 | π/6 | π/9 | π/12 | π/4 |
Приложение 1
Задача 6 [5, с. 43].
Рассчитать сварные швы хомута с двутавровой балкой и подобрать сечение хомута : b х δ (рис. 6).
Материал хомута – сталь Ст. 3.
F – усилие, приложенное к хомуту. Нагрузка статическая.
Сварка ручная.
Рисунок 1.6 – Сварное соединение хомута с двутавровой балкой
Таблица 1.6– исходные данные к расчетам
Параметры | Варианты исходных данных | |||||||||
1 | 2 | 3 | 4 | 5 | 6 | 7 | 8 | 9 | 10 | |
F , кН | 110 | 120 | 130 | 140 | 150 | 160 | 170 | 180 | 190 | 200 |
Приложение 1
Задача 7.
Проверить прочность клёпаного соединения уголков с косынкой.
F – усилие, приложенное к уголкам. Нагрузка статическая.
Материал деталей конструкции – сталь Ст. 3.
Рисунок 1.7 – Клепаное соединение
Таблица 1.7 – исходные данные к расчетам
Параметры | Варианты исходных данных | |||||||||
1 | 2 | 3 | 4 | 5 | 6 | 7 | 8 | 9 | 10 | |
F , кН | 450 | 260 | 350 | 280 | 320 | 360 | 400 | 300 | 250 | 420 |
L , мм | 1000 | 500 | 700 | 650 | 950 | 550 | 600 | 750 | 900 | 850 |
δ, мм | 15 | 20 | 10 | 15 | 12 | 10 | 20 | 15 | 12 | 10 |
Приложение 1
Задача 8 [5, с. 43].
Рассчитать заклепки, крепящие скобы «А» к косынке «В» и косынку к швеллеру «С» (рис. 1.8).
2F – сила, приложенная к блоку. Нагрузка статическая.
Материал деталей конструкции — сталь Ст. З.
Рисунок 1.8 – Клепаное соединение
Таблица 1.8 – исходные данные к расчетам
Параметры | Варианты исходных данных | |||||||||
1 | 2 | 3 | 4 | 5 | 6 | 7 | 8 | 9 | 10 | |
F, кН |