Изломы образцов на растяжение
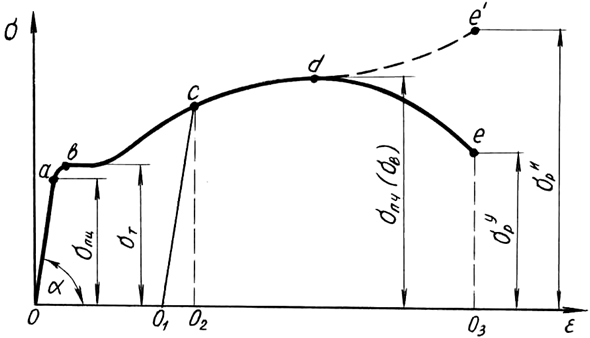
Лабораторная работа № 1
Цель работы – изучить поведение малоуглеродистой стали при растяжении и определить ее механические характеристики.
Основные сведения
Испытания на растяжение являются основным и наиболее распространенным методом лабораторного исследования и контроля механических свойств материалов.
Эти испытания проводятся и на производстве для установления марки поставленной заводом стали или для разрешения конфликтов при расследовании аварий.
В таких случаях, кроме металлографических исследований, определяются главные механические характеристики на образцах, взятых из зоны разрушения конструкции. Образцы изготавливаются по ГОСТ 1497-84 и могут иметь различные размеры и форму (рис. 1.1).
Рис. 1.1. Образцы для испытания на растяжение
Между расчетной длиной образца lо и размерами поперечного сечения Ао (или dо для круглых образцов) выдерживается определенное соотношение:
В испытательных машинах усилие создается либо вручную — механическим приводом, либо гидравлическим приводом, что присуще машинам с большей мощностью.
В данной работе используется универсальная испытательная машина УММ-20 с гидравлическим приводом и максимальным усилием 200 кН, либо учебная универсальная испытательная машина МИ-40КУ (усилие до 40 кН).
Порядок выполнения и обработка результатов
Образец, устанавливаемый в захватах машины, после включения насоса, создающего давление в рабочем цилиндре, будет испытывать деформацию растяжения. В измерительном блоке машины есть шкала с рабочей стрелкой, по которой мы наблюдаем рост передаваемого усилия F.
Зависимость удлинения рабочей части образца от действия растягивающей силы во время испытания отображается на миллиметровке диаграммного аппарата в осях F-Δl (рис. 1.2).
В начале нагружения деформации линейно зависят от сил, потому участок I диаграммы называют участком пропорциональности. После точки В начинается так называемый участок текучести II.
На этой стадии стрелка силоизмерителя как бы спотыкается, приостанавливается, от точки В на диаграмме вычерчивается либо прямая, параллельная горизонтальной оси, либо слегка извилистая линия — деформации растут без увеличения нагрузки. Происходит перестройка структуры материала, устраняются нерегулярности в атомных решетках.
Далее самописец рисует участок самоупрочнения III. При дальнейшем увеличении нагрузки в образце происходят необратимые, большие деформации, в основном концентрирующиеся в зоне с макронарушениями в структуре – там образуется местное сужение — «шейка».
На участке IV фиксируется максимальная нагрузка, затем идет снижение усилия, ибо в зоне «шейки» сечение резко уменьшается, образец разрывается.
При нагружении на участке I в образце возникают только упругие деформации, при дальнейшем нагружении появляются и пластические — остаточные деформации.
Если в стадии самоупрочнения начать разгружать образец (например, от т. С), то самописец будет вычерчивать прямую СО1. На диаграмме фиксируются как упругие деформации Δlу (О1О2), так и остаточные Δlост (ОО1). Теперь образец будет обладать иными характеристиками.
Так, при новом нагружении этого образца будет вычерчиваться диаграмма О1CDЕ, и практически это будет уже другой материал. Эту операцию, называемую наклеп, широко используют, например, в арматурных цехах для улучшения свойств проволоки или арматурных стержней.
Диаграмма растяжения (рис. 1.2) характеризует поведение конкретного образца, но отнюдь не обобщенные свойства материала. Для получения характеристик материала строится условная диаграмма напряжений, на которой откладываются относительные величины – напряжения σ=F/A0 и относительные деформации ε=Δl/l0 (рис. 1.3), где А0, l0 – начальные параметры образца.
Рис. 1.2. Диаграмма растяжения образца из малоуглеродистой стали
Рис. 1.3. Условная диаграмма напряжений при растяжении
Условная диаграмма напряжений при растяжении позволяет определить следующие характеристики материала (рис. 1.3):
σпц – предел пропорциональности – напряжение, превышение которого приводит к отклонению от закона Гука. После наклепа σпц может быть увеличен на 50-80%;
σу – предел упругости – напряжение, при котором остаточное удлинение достигает 0,05%. Напряжение σу очень близко к σпц и обнаруживается при более тонких испытаниях. В данной работе σу не устанавливается;
σт – предел текучести – напряжение, при котором происходит рост деформаций при постоянной нагрузке.
Иногда явной площадки текучести на диаграмме не наблюдается, тогда определяется условный предел текучести, при котором остаточные деформации составляют ≈0,2% (рис. 1.4);
Рис. 1.4. Определение предела упругости и условного предела текучести
σпч (σв) – предел прочности (временное сопротивление) – напряжение, соответствующее максимальной нагрузке;
σр – напряжение разрыва. Определяется условное σур и истинное σир=Fр/Аш, где Аш – площадь сечения «шейки» в месте разрыва.
Определяются также характеристики пластичности – относительное остаточное удлинение
δ = (l1 – l0)∙100% / l0,
где l1 – расчетная длина образца после разрыва,
и относительное остаточное сужение
ψ = (А0 — Аш)∙100% / А0.
По диаграмме напряжений можно приближенно определить модуль упругости I рода
E=σпц/ε=tgα,
причем после операции наклепа σпц возрастает на 20-30%.
Работа, затраченная на разрушение образца W, графически изображается на рис. 1.2 площадью диаграммы OABDEO3. Приближенно эту площадь определяют по формуле:
W = 0,8∙Fmax∙Δlmax.
Удельная работа, затраченная на разрушение образца, говорит о мере сопротивляемости материала разрушению w = W/V, где V = A0∙l0 – объем рабочей части образца.
По полученным прочностным и деформационным характеристикам и справочным таблицам делается вывод по испытуемому материалу о соответствующей марке стали
Контрольные вопросы
- Изобразите диаграмму растяжения образца из малоуглеродистой стали (Ст.3). Покажите полные, упругие и остаточные абсолютные деформации при нагружении силой, большей, чем Fт.
- На каком участке образца происходят основные деформации удлинения? Как это наблюдается на образце? Какие нагрузки фиксируются в этот момент?
- Объясните, почему после образования шейки дальнейшее растяжение происходит при все уменьшающейся нагрузке?
- Перечислите механические характеристики, определяемые в результате испытаний материала на растяжение. Укажите характеристики прочности и пластичности.
- Дайте определение предела пропорциональности.
- Дайте определение предела упругости.
- Дайте определение предела текучести.
- Дайте определение предела прочности.
- Как определить предел текучести при отсутствии площадки текучести? Покажите, как это сделать, по конкретной диаграмме.
- Какие деформации называются упругими, какие остаточными? Укажите их на полученной в лабораторной работе диаграмме растяжения стали.
- Как определяется остаточная деформация после разрушения образца?
- Выделите на диаграмме растяжения образца из мягкой стали упругую часть его полного удлинения для момента действия максимальной силы.
- Какое явление называется наклепом? До какого предела можно довести предел пропорциональности материалов с помощью наклепа?
- Как определяется работа, затраченная на разрушение образца? О каком свойстве материала можно судить по удельной работе, затраченной на разрушение образца?
- Как определить марку стали и допускаемые напряжения для нее после проведения лабораторных испытаний?
- Чем отличается диаграмма истинных напряжений при растяжении от условной диаграммы?
- Можно ли определить модуль упругости материала по диаграмме напряжений?
- Как определить работу, затрачиваемую на деформации текучести лабораторного образца?
Испытание материалов на сжатие >
Краткая теория >
Примеры решения задач >
Источник
Разрушающий контроль – исследование качества сварного соединения по воздействию на материал, при котором происходит разрушение контрольного образца. Испытания чаще всего проводят на образцах-свидетелях, сваренных из того же материала, как у изделия, и по такой же технологии.
Результатом проведения разрушающего контроля является получение числовых данных, характеризующих прочность и надежность сварного соединения. Разрушающий контроль регламентируется государственными нормативами и подразделяется на виды контроля.
Методы контроля
Разрушающие исследования включают методы испытания сварных образцов:
- механические;
- металлографические;
- коррозионные.
Механические испытания
Контроль предназначен для определения механических свойств материалов. Цель – проверка соответствия механических качеств конструкции запросам технических условий или проекта. Для проведения эксперимента из изделия вырезают контрольный образец или вместе с основной конструкцией сваривают контрольную пластину.
Механические испытания сварных соединений, согласно ГОСТ 6996-66, включают проверку:
- на растяжение;
- ударный изгиб.
Контроль также предусматривает определение твердости металла различных участков сварного шва и исследование соединения на стойкость против механического старения.
По характеру приложения нагрузки механические испытания разделяют на виды:
- статические – для них характерна малая скорость деформации контрольного образца в результате воздействия статической нагрузки (растяжение, сжатие);
- динамические – проверка воздействия на испытуемый предмет нагрузки, изменяемой с большой скоростью (ударный изгиб);
- на усталость – выявление способности металла сопротивляться воздействию много раз повторяющихся переменных нагрузок, изменяющихся по направлению, времени и величине (изгиб, растяжение, кручение).
Статическое растяжение
Испытание проводится способом растяжения (разрыва) образцов и заключается в определении следующих механических свойств исследуемого материала:
- пределов пропорциональности, текучести и упругости;
- предела прочности (временного сопротивления);
- истинного сопротивления разрыву;
- относительных удлинения и сужения после разрыва.
Работа выполняется на специальных машинах, оборудованных приборами автоматической записи диаграммы растяжения. Проверяют образцы прямоугольного или круглого сечения (диаметр 3-10 мм).
Ударный изгиб
Для проведения испытаний применяют прямоугольные или квадратные образцы с односторонним надрезом. Надрез в зависимости от назначения контрольного эксперимента может располагаться:
- на линии сплавления;
- в зоне термического влияния;
- на оси сварного шва.
Цель испытания – определение ударной вязкости исследуемого металла при заданной температуре в зоне соединения.
Ударная вязкость надрезанного образца определяется отношением работы, затраченной на излом контрольного элемента (в Дж), к площади его поперечного сечения в зоне надреза до проведения испытания (в м2 ).
После проведения испытания выполняется исследование структуры излома. Цель – определение наличия дефектов сварного шва и степени кристалличности на изломе.
Металлографические исследования
Цель – определение структуры материала сварного соединения. Исследованием устанавливают:
- правильность выбора всех факторов, влияющих на качество сварного шва;
- дефекты шва и причины их возникновения.
Металлографический анализ включает макроструктурное и микроструктурное исследования материала сварного шва.
Макроструктурный метод
Служит для предварительной оценки качества сварного соединения. Макроструктуру шва на поверхности образца (шлифе и изломе сварного шва) можно наблюдать визуально или при двадцатикратном увеличении. Вырезанные темплеты для шлифов шлифуют и травят реактивами, подбираемыми в зависимости от типа металла и цели исследования.
Исследованием выявляют:
- строение, размеры и форму шва;
- наличие дефектов (трещины, непровары, газовые поры, шлаковые включения, усадочные рыхлости).
Макроструктуру материала также изучают по излому, внешний вид которого говорит о характере разрушения металла. Излом крупнозернистый с характерным блеском указывает на хрупкость металла. Серый волокнистый излом, имеющий матовую поверхность, свидетельствует о хорошей пластичности материала.
Микроструктурный метод
Предполагает исследование микроструктуры металла – строения металла, видимого под микроскопом. Анализ проводят на шлифах с отполированной и отшлифованной до блеска поверхностью, протравленной специальными растворами.
Исследование проводится с применением оптического микроскопа при увеличениях от 50 до 2000 раз. Микроструктурным методом устанавливаются:
- качество обработки шлифа;
- наличие газовых пор и окисных пленок;
- наличие микротрещин;
- степень загрязнения металла сварного шва неметаллическими включениями.
Неметаллические включения могут быть разной формы и проявляются на белом фоне шлифа темными пятнами. Микротрещины выглядят тонкими извилистыми кривыми. Газовые поры – черными пятнами.
( 1 оценка, среднее 5 из 5 )
Источник
Оценка результатов
испытания
Предел текучести sS0 определяется по формуле
sS0 = FS/A(Н/мм2), (2)
где fso — сила при верхнем пределе
текучести; А0— площадь первоначального поперечного сечения
образца.
Необходимую для расчета
предела текучести силу FSoможно определить в процессе испытания по показанию
силоизмерителя
6
Рис. 24. Примеры
различных форм верхнего (sS0) и нижнего sSUпределов текучести
испытательной машины или
после проведения испытания — по диаграмме растяжения. На предел текучести
влияют многие факторы, например форма образца, условия испытания, жесткость
испытательной машины, испытываемый материал и его структура. Поэтому форма
кривой сила — удлинение может быть самой разнообразной (рис. 24). Обычно
определяют верхний предел текучести.
Предел прочности
образца на растяжение (Н/мм2):
sв= Fmax/A, (3)
тде Fmax— максимальная нагрузка в
процессе испытания.
Необходимую для расчета
предела прочности при растяжении максимальную ‘нагрузку Ртшможно
определить по показанию контрольной стрелки (показателя максимума) или по
диаграмме растяжения.
Предел прочности в момент
разрыва sR вычисляется по формуле (Н/мм2):
(4)
где FR— нагрузка в момент разрушения
образца, которая определяется по показанию силоизмерителя в процессе испытания
или по диаграмме растяжения (при наличии точного регистрирующего устройства).
Найденные прочностные характеристики указываются с точностью, зависящей от их
величины (в Н/мм2): до 200 — ±1; 200—500 — ±2; 500—1000 — ±5. Относительное
удлинение при разрыве
(5)
где L0 и LB— расчетные длины образца до и после испытаний.
Для нахождения LB обе части разрушенного образца
складываются таким образом, чтобы они образовали одно целое. Расстояние между
крайними рисками замеряется с точностью до 0,1 мм. Значения относительного удлинения, определенные на коротких или длинных образцах,
обозначаются соответственно б5 и 610. В том случае, если
место излома расположено вне требуемых границ, для определения относительного
удлинения используется способ корректировки [1].
На расчетной длине
образца N перед испытанием наносят обычно 10—20 делений на равных расстояниях
друг от друга (см. рис. 25). После испытания последнее деление более короткой
части образца обозначается буквой А, а деление более длинной части,
расположенное по возможности на таком же расстоянии от места разрушения, что и
деление A, обозначается буквой В. Если n — число делений между A и В, то относительное удлинение (%)
можно определить следующим образом:
(6)
• (7)
У пластмасс подобного
вида корректировка удлинения не является обычной. В отличие от металлических
материалов у высокополимерных материалов (например, полиэтилена) определяют
удлинение при разрыве, соответствующее пределу прочности при разрыве. Удлинение
при разрыве
(8)
для расчета удлинения при
разрыве необходимо, чтобы уже в процессе испытания на растяжение изменение
расчетной длины ∆LR
определялось в момент разрыва образца с помощью штангенциркуля.
Относительное сужение
при разрыве
(9)
гдеАв—
минимальная площадь поперечного сечения образца после испытаний.
Для определения
минимальной площади поперечного сечения образца после испытания Авнужно с помощью штангенциркуля на плоскости излома замерить его наименьший
диаметр dB или наименьшую толщину и ширину (в случае
плоского образца) с точностью до 0,1 мм.
Значения относительного
удлинения, удлинения при разрыве и относительного сужения при разрыве в
зависимости от их величины следует указывать со следующей точностью, %: до 10
— 0,2; от 10 до 20 — 0,5; от 20 до 50 — 1,0; свыше 50 — 2,0,
Вычисленные значения
прочностных и механических характеристик нужно записать в таблицу.
Описание картины
излома
Картина излома и его
форма дают важные сведения о поведении материала под действием одноосной
растягивающей нагрузки. Уже визуальное наблюдение поверхности излома позволяет
Рис. 25. Определение
удлинения при разрушении
выяснить, сопровождалось
ли разрушение образца четко выраженной пластической деформацией, или произошел
макроскопический хрупкий излом. Типичные для образцов на растяжение формы
излома представлены на рис. 25. С помощью этих примеров можно провести оценку
картин излома исследованных материалов, схематически изобразить и кратко
описать их в протоколе испытания.
Сравнение диаграмм
растяжения
Необходимо отобрать
типичные диаграммы растяжения и занести их в протокол испытания. При этом
кривые нагрузка — удлинение чистого алюминия, стали С15, чугуна с пластинчатым
графитом и полиэтилена, а также армко-железа, сталей С45 и С60 надо представить
с учетом модуля упругости Е соответственно на одной диаграмме.
Характерные различия -диаграмм растяжения должны быть, кроме того, описаны
словесно.
Источник
Как правило, испытание материалов на прочность применяется для выяснения причин и прогнозирования отказов. Для прогнозирования режима отказа важно понимать истинные условия нагрузки и реальные режимы отказа (то, что, в конечном счете, оказывает влияние на продукт при использовании). Как мы уже говорили в пособии «Наука тестирования соединений» (ориг. Science of Bond Testing), зачастую сделать это не так уж просто. В то время как режим отказа обычно известен или, по крайней мере, предсказуем, истинное условие нагрузки может быть непонято.
В случае, если условия истинной нагрузки неизвестны или под вопросом, главной целью тестирования является воспроизведение «Исследуемого режима отказа» (Failure Mode of Interest). Независимо от того, насколько правильно, как мы полагаем, нам удалось добиться условий истинной нагрузки, если при тестировании не создается реальный режим отказа, который нас интересует, какую ценность имеет данное тестирование? Любое тестирование, которое действительно вызывает интересуемый режим отказа, напротив, вероятно, будет полезно.
Когда истинная нагрузка известна, ее следует попробовать применить и создать истинный режим отказа. Если полученный результат не будет соответствовать интересуемому режиму отказа, определенная истинная нагрузка, режим отказа или оба параметра неверны.
Рис.3 Схематичное изображение испытания при трёхточечном изгибе
При данном виде тестирования образец подвергается изгибающему моменту, показанному на графике. Изгибающий момент увеличивается с постоянной скоростью в двух опорных точках от нуля до максимума, где применяется нагрузка F. Следует отметить, что на приведенном рисунке показан стандартный луч, однако те же принципы применяются, когда величина b намного больше, чем величина h, как в случае с кристаллом или пластиной.
Как видно из рисунков, изгибающий момент создает растягивающую нагрузку на нижнюю часть и сжимающую нагрузку на верхнюю часть испытываемого образца. При тестировании хрупких материалов и если возникает проблема распространения трещин, наиболее вероятным может быть отказ вследствие применения растягивающей нагрузки. Если одна сторона ваших образцов более подвержена воздействию растягивающей нагрузки, при тестировании изделие следует размещать таким образом, чтобы нагрузка F прилагалась к обратной стороне.
Рис.3 Схематичное изображение испытания при трёхточечном изгибе
При данном виде тестирования образец подвергается изгибающему моменту, показанному на графике. Изгибающий момент увеличивается с постоянной скоростью в двух опорных точках от нуля до максимума, где применяется нагрузка F. Следует отметить, что на приведенном рисунке показан стандартный луч, однако те же принципы применяются, когда величина b намного больше, чем величина h, как в случае с кристаллом или пластиной.
Как видно из рисунков, изгибающий момент создает растягивающую нагрузку на нижнюю часть и сжимающую нагрузку на верхнюю часть испытываемого образца. При тестировании хрупких материалов и если возникает проблема распространения трещин, наиболее вероятным может быть отказ вследствие применения растягивающей нагрузки. Если одна сторона ваших образцов более подвержена воздействию растягивающей нагрузки, при тестировании изделие следует размещать таким образом, чтобы нагрузка F прилагалась к обратной стороне.
Изгибающий момент и напряжение при изгибе
Переход от сжатия к растяжению, проходящий через толщину h, приводит к напряжению сдвига также по всей толщине образца. Напряжение сдвига применяется в тех случаях, когда пользователь опасается отслоения в конечном изделии, это напряжение воздействует на ламинарные слои и соединения и тем самым проверяет их прочность. В тех случаях, когда проверяемые слои находятся близко к поверхности изделия, относительное расширение и сжатие между слоями можно не применять, протестировав образец лицевой стороной вниз или вверх. Напряжение сдвига будет одинаковым, однако относительное расширение в сравнении с усадкой, наблюдаемой между слоями изменится на противоположное. Если слой находится в середине толщины при h/2 и нейтральной оси, все напряжения будут равны нулю. Это делает отказ менее вероятным, но из-за различий между теоретической моделью и реальным миром, например из-за несимметрии испытание на изгиб может быть полезно.
Рис.5 При тестировании на изгиб может возникать расслоение.
Трехточечный изгиб чаще всего применяется при однократной нагрузке, но чтобы проверить усталость и распространение трещин нагрузку также можно применять много раз.
Испытание при четырёхточечном изгибе
Рис.6 На графике показан разрез чистого изгиба при локальном напряжении при нагрузке по опорным точкам
Испытание при четырёхточечном изгибе имеет много общего с испытанием при трёхточечном изгибе, однако как Вы можете видеть из рисунка изгибающий момент на графике совершенно другой. Изгибающий момент снова увеличивается с постоянной скоростью до точки приложения нагрузки, в данном случае двух точек, но с постоянным изгибающим моментом между ними. Это очень важное и полезное отличие, а во многих случаях более близкое к истинному состоянию нагрузки. Например, если согнуть собранную солнечную панель, на отдельные пластины может воздействовать только постоянный изгиб. Испытание при четырёхточечном изгибе дает Вам возможность тестировать участок образца на постоянный и максимальный изгиб. В случае испытания при трёхточечном изгибе, максимальный изгиб применяется только в одной точке и, как мы увидим, имеет другие осложнения.
Растягивающая нагрузка также находится на нижней стороне, в пределах толщины есть сдвиг, на края нет нагрузки, и испытание может быть выполнено с применением как однократной, так и многократной нагрузок.
Применение точки нагрузки
Рис. 7 Точечная нагрузка при испытании на изгиб
На поверхностях, в которых, тестируемый образец поддерживается и куда прикладывается нагрузка, возникает местное напряжение. В то время как анализ ранее упомянутых изгибающих моментов выполнить относительно просто, эти нагрузки вычислить бывает сложно. Хотя они могут быть незначительными, если тестирование обеспечивает условие нагрузки на изгиб и/или режимы отказа, которые вас интересуют. Это ясно показывает преимущества испытания при четырёхточечном изгибе, когда часть испытываемого образца подвергается максимальной изгибающей силе независимо от местных напряжений, в отличие от испытания при трёхточечном изгибе, когда местная нагрузка применяется только в одной точке максимального изгибающего момента.
И наоборот, такие точки местного напряжения могут быть близки к истинной нагрузке или обеспечивать представляющий интерес режим отказа. В этом случае, мы получаем точечную нагрузку, которая может быть достигнута в результате тестирования на изгиб, которое Вас интересует, и тогда испытание при трёхточечном изгибе может быть идеальным. Тем не менее, оно показывает сочетание местного напряжения и изгибающей силы. Если Вас интересуют только местные «разламывающие» напряжения при приложении нагрузки в точке или области, лучшим решением может быть обеспечить полную поддержку образца на жесткой и плоской поверхности; в данном случае это будет уже не испытание на изгиб.
Напряжения при местной нагрузке могут быть смоделированы с использованием метода исследования конечных элементов (Finite Element Analysis).
Рис. 8 Тестирование на разрушение
Испытание на изгиб методом кольца и шара
Рис.9 Испытание на изгиб методом кольца и шара
В сечении по диаметру (или радиусу) испытание шаром и кольцом может считаться аналогичным испытанию при трёхточечном изгибе, здесь так же применяются две опорные точки и одна точку приложения нагрузки. Однако, испытание испытанию при трёхточечном изгибе является двумерным так, как напряжение на изгиб можно рассматривать в одной плоскости, такой как показанная на графиках изгибающего момента при трехточечном и четырехточечном изгибе. При испытании методом кольца нагрузка прилагается как в радиальной, так и в нормальной плоскости. Возможно, вы сможете отчетливо представить себе это, поскольку тестируемый образец сгибается вдоль линий радиуса/диаметра и растягивается вдоль круговых линий, центрированных вокруг точки нагрузки. Они называются радиальными и окружными напряжениями. Радиальные напряжения аналогичны напряжениям изгиба при трехточечном и четырехточечном изгибе. Окружные напряжения аналогичны крутящим моментам, вызванным коэффициентом Пуассона, отличие составляет то, что они не равны нулю на углах/краях образца.
Подобно испытанию при трёхточечном изгибе, максимальное напряжение в испытании методом кольца и шара происходит там, где применяется нагрузка. Так же, как в испытании при трёхточечном изгибе радиальные напряжения равны нулю на краях испытываемого образца, отличие составляет то, что на края воздействуют значительные круговые напряжения. Эта особенность делает данный метод испытания пригодным для проверки таких явлений, как трещины, причины неровностей/напряжения и остаточные производственные напряжения, возникающие на краях образца. Типичным примером таких неровностей являются трещины/разломы, возникающие во время резки.
Рис. 10 Трещины при напряжении у кромок подложки.
Испытание на изгиб методом кольца и кольца
Рис.11 Испытание на изгиб методом кольца и кольца
Сходство и различия которые наблюдаются между испытанием на изгиб методом кольца и шара и испытанием при испытанию при трёхточечном изгибе также имеют место между испытанием на изгиб методом кольца и кольца и испытанием при четырёхточечном изгибе. При испытании на изгиб методом кольца и кольца круговое растягивающее напряжение воздействует на края испытуемого образца и, таким образом становится возможным испытание краевых эффектов. Как и в случае испытания при четырёхточечном изгибе, в пределах меньшего кольца наблюдаются постоянне напряжения изгибающего момента, которые включают в себя постоянное окружное напряжение. Поскольку испытание на изгиб методом кольца и кольца распределяет приложенную нагрузку, местные напряжения уменьшаются, что снижает вероятность сбоя при приложении нагрузки.
Все, описанные в данной статье методы тестирования могут быть выполнены на установках тестирования соединений Condor Sigma, компании XYZTEC (Голландия). Более подробную информацию о данных установках Вы можете получить нашем сайте по следующей ссылке.
Также Вы можете просмотреть видеоматериалы об испытании при трёхточечном изгибе:
И испытании при четырёхточечном изгибе
Узнать о других видах тестирования и наиболее выгодных условиях приобретения установок линейки Condor Sigma можно у наших менеджеров, направив официальный запрос.
Источник