Испытание арматуры на растяжение
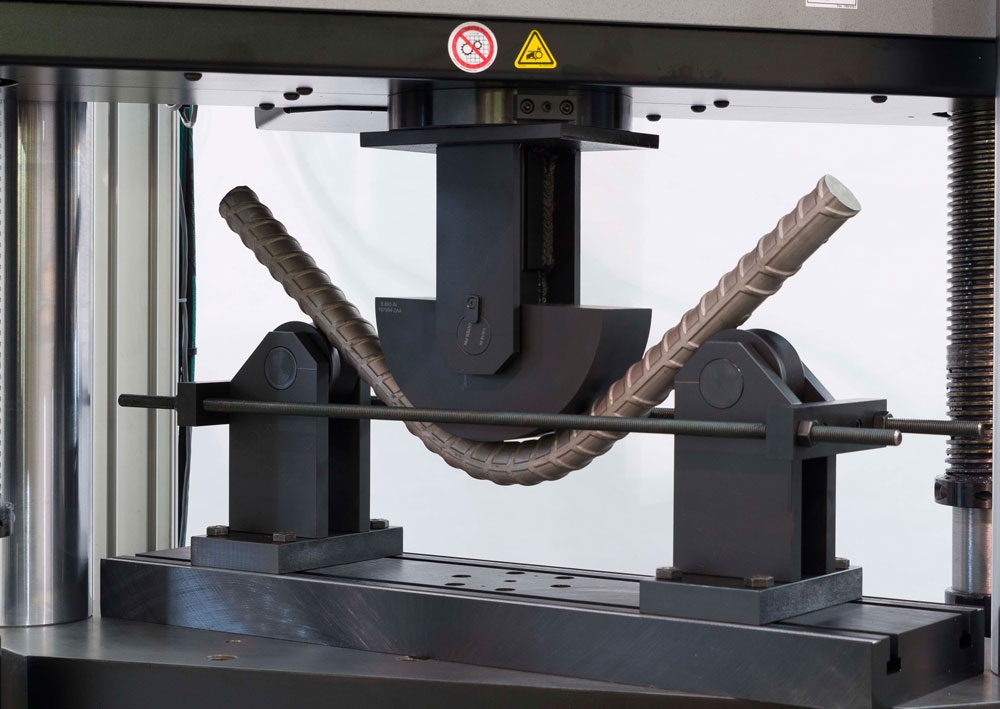

КАТЕГОРИИ:
Архитектура-(3434)Астрономия-(809)Биология-(7483)Биотехнологии-(1457)Военное дело-(14632)Высокие технологии-(1363)География-(913)Геология-(1438)Государство-(451)Демография-(1065)Дом-(47672)Журналистика и СМИ-(912)Изобретательство-(14524)Иностранные языки-(4268)Информатика-(17799)Искусство-(1338)История-(13644)Компьютеры-(11121)Косметика-(55)Кулинария-(373)Культура-(8427)Лингвистика-(374)Литература-(1642)Маркетинг-(23702)Математика-(16968)Машиностроение-(1700)Медицина-(12668)Менеджмент-(24684)Механика-(15423)Науковедение-(506)Образование-(11852)Охрана труда-(3308)Педагогика-(5571)Полиграфия-(1312)Политика-(7869)Право-(5454)Приборостроение-(1369)Программирование-(2801)Производство-(97182)Промышленность-(8706)Психология-(18388)Религия-(3217)Связь-(10668)Сельское хозяйство-(299)Социология-(6455)Спорт-(42831)Строительство-(4793)Торговля-(5050)Транспорт-(2929)Туризм-(1568)Физика-(3942)Философия-(17015)Финансы-(26596)Химия-(22929)Экология-(12095)Экономика-(9961)Электроника-(8441)Электротехника-(4623)Энергетика-(12629)Юриспруденция-(1492)Ядерная техника-(1748)
Арматурная сталь (далее арматура) для армирования железобетонных конструкций по своим физико-механическим характеристикам подразделяется на классы: А-1 (А240), A-II (А300), A-III (A400), A-IV (A500), A-V (А800) А-VI (А1000), арматурная проволока Вр-1, высокопрочная проволока Вр-II, канаты К-7, К-19. Термически и термомеханически упрочненные стали обозначают индексом Ат, свариваемую сталь – АтС. Арматуру для районов Севера обозначают АС.
По профилю поверхности стержня арматуру подразделяютна гладкую AI (А240) и периодического профиля. По технологии изготовления подразделяют на горячекатаную и холоднотянутую. Арматурную сталь изготавливаютиз углеродистой и низколегированной стали марок, приведенных в табл. 5.1. Марка стали указывается потребителем в заказе. При отсутствии таких указаний марку стали устанавливает предприятие-изготовитель.
Таблица 5.1
Марки углеродистой и низколегированной стали
Класс арматурной стали | Диаметр профиля, мм | Марка стали |
А-1 (А240) | 6–40 | СтЗкп, СтЗпс, СтЗсп |
A-II (А300) | 10–40 10–80 | Ст5сп, Ст5пс 1НГ2С |
Ас-11 (Ас300) | 10–32 (36–40) | 10ГТ |
A-III (A400) | 6–40 6–22 | 35ГС, 25Г2С 32Г2Рпс |
A-IV (A600) | 10–18 (6–8) 10–32 (36-40) | 80С 20ХГ2Ц |
A-V (A800) | (6–8) 10–32 (36–40) | 23Х2Г2Т |
A-VI (A1000) | 10–22 | 22Х2Г2АЮ, 22Х2Г2Р, 20Х2Г2СР |
Для стержней класса A-VI (А 1000) марки стали устанавливают по согласованию изготовителя с потребителем.
Допускается изготовление арматуры класса A-V (A800) из стали марок 22Х2Г2АЮ, 22Х2Г2Р и 20Х2Г2СР.
Размеры, указанные в скобках, используют по согласованию изготовителя с потребителем.
Химический состав арматурной углеродистой стали должен соответствовать ГОСТ 380–94, низколегированной стали – нормам, приведенным в табл. 5.2.
Таблица 5.2
Марки низколегированной стали
Марки стали | Массовая доля элементов, % | ||||||
Углерод | Марганец | Кремний | Хром | ||||
10ГТ 18Г2С 32Г2Рпс 35ГС 25Г2С 20ХГ2Ц 23Х2Г2Т | Не более 0,13 0,14–0,23 0,28–0,37 0,30–0,37 0,20–0,29 0,19–0,26 0,74–0,82 0,19–0,26 0,19–0,26 0,19–0,26 0,16–0,26 | 1,00–1,40 1,20–1,60 1,30–1,75 0,80–1,20 1,20–1,60 1,50–1,90 0,50–0,90 1,40–1,70 1,40–1,70 1,50–1,90 1,40–1,80 | 0,45–0,65 0,60–0,90 Не более 0,17 0,60–0,90 0,60–0,90 0,40–0,70 0,60–1,10 0,40–0,70 0,40–0,70 0,40–0,70 0,75–1,55 | Не более 0,30 Не более 0,30 Не более 0,30 Не более 0,30 Не более 0,30 0,90–1,20 Не более 0,30 1,35–1,70 1,50–2,10 1,50–1,90 1,40–1,80 | |||
Марки стали | Титан | Цирко- ний | Алюминий | Никель | Сера | Фосфор | Медь |
10ГТ | 0,015–0,035 | – | 0,02–0,05 | 0,30 | 0,0–10 | 0,030 | 0,30 |
18Г2С | – | – | – | 0,30 | 0,045 | 0,040 | 0,30 |
32Г2Рпс | – | – | 0,001–0,015 | 0,30 | 0,050 | 0,045 | 0,30 |
35ГС | – | – | – | 0,30 | 0,045 | 0,040 | 0,30 |
25Г2С | – | – | – | 0,30 | 0,045 | 0,040 | 0,30 |
20ХГ2Ц | – | 0,05–0,14 | – | 0,30 | 0,045 | 0,045 | 0,30 |
80С | 0,015–0,040 | – | – | 0,30 | 0,045 | 0,040 | 0.30 |
23Х2Г2Т | 0,02–0,08 | – | 0,015–0,050 | 0,30 | 0,045 | 0,045 | 0,30 |
22Х2Г2АЮ | 0,005–0,030 | – | 0,02–0,07 | 0,30 | 0,040 | 0,040 | 0,30 |
22Х2Г2Р | 0,02–0,08 | – | 0,015–0,050 | 0,30 | 0,040 | 0,040 | 0,30 |
20Х2Г2СР | 0,02–0,08 | – | 0,05–0,050 | 0,30 | 0,040 | 0,040 | 0,30 |
10ГТ | 0,015–0,035 | – | 0,02–0,05 | 0,30 | 0,0–10 | 0,030 | 0,30 |
В соответствии с ГОСТ 5781-82 при испытании арматуры определяют следующие показатели:
– диаметр;
– класс арматуры;
–прочность на растяжение;
– прочность на изгиб;
– прочность на перегиб.
Диаметр арматуры. Диаметр гладкой арматуры определяют штангенциркулем с точностью до 0,1 мм. Площадь поперечного сечения арматуры периодического профиля А, мм2, вычисляют по формуле
(5.1)
где т – масса испытуемого образца кг; l – длина испытуемого образца, м; ρ – плотность стали, 7850 кг/м3.
Для практических целей диаметр арматуры периодического профиля можно определить как усредненный диаметр арматуры между ребер и по ребрам, приведенный к сортаменту.
Класс арматуры. Класс арматуры определяют по результатам испытания образцов на растяжение путем сравнения величин полученных характеристик с нормируемыми значениями, указанными в ГОСТ 5781, ГОСТ 10884, ГОСТ 7348.
К нормируемым характеристикам относят: предел текучести , временное сопротивление разрыву и относительное удлинение .
Испытание арматуры на растяжение. Испытание арматуры на растяжение проводят в соответствии с ГОСТ 12004 «Сталь арматурная. Методы испытания на растяжение».
Для испытания на растяжение применяют образцы арматуры круглого или периодического профиля с необработанной поверхностью номинальным диаметром от 3,0 до 80 мм. Образцы отбирают по акту отбора из различных стержней одной партии. Допускается проводить испытания образцов горячекатаной стержневой арматуры номинальным диаметром более 20мм на обточенных образцах цилиндрической формы с головками, по возможности с сохранением на головках поверхности проката. Полная длина образца арматуры выбирается в зависимости от рабочей длины и конструкции захвата испытательной машины.
Рабочая длина образца должна составлять:
– для образца с номинальным диаметром до 20 мм включительно – не менее 200 мм;
– для образца с номинальным диаметром свыше 20 мм – не менее 10d;
– для арматурных канатов всех диаметров – не менее 350 мм.
При испытании определяют следующие механические свойства:
– относительное удлинение после разрыва %;
– временное сопротивление , МПа (кгс/мм2);
– предел текучести (физический) , МПа (кгс/мм2);
– предел текучести и упругости (условные).
Зависимость деформации стали от напряжения в арматуре различных классов приведена на рис. 5.1.
Испытание на растяжения проводят на гидравлических разрывных машинах типа Р50. Средняя скорость нагружения при испытании до предела текучестине должна быть более 10 МПа (1 кгс/мм2) в секунду; за пределом текучести скорость нагружения может быть увеличена так, чтобы скорость перемещения подвижного захвата машины не превышала 0,1 рабочей длины испытуемого образца в минуту; шкала силоизмерителя испытательной машины не должна превышать пятикратного ожидаемого значения наибольшей нагрузки Р для испытываемого образца арматуры.
Рис. 5.1 Зависимость деформации от напряжения
в арматуре классов А-I, А-III, Ат-V
При определении условных пределов упругости и текучести с помощью тензометра относительная длина деления шкалы тензометра не должна превышать:
– 0,005 % базы тензометра при определении
– 0,05 % базы тензометра при определении
Перед испытанием образец на длине, больше рабочей длины образца (обычно расстояние между захватами), размечается на п равных частей при помощи меток, наносимых делительной машиной, скобками или керном. Расстояние между метками для арматуры диаметром 10 мм и более не должно превышать величину d и быть кратным 10 мм. Для арматуры диаметром менее 10 мм расстояние между метками принимается равным 10 мм. Допускается при разметке образцов расстояние между метками принимать более 10 мм и превышающим величину d, но не более величины начальной расчетной длины /д.
Величину относительного удлинения %, вычисляют по формуле
(5.2)
где l0 – начальная расчетная длина, равная 5d, 100 мм и далее кратная 100 мм.
В зависимости от величины начальной расчетной длины к букве добавляют индекс. Например, при начальной расчетной длине, равной 5d, – при 100 мм – и т.д.
Конечную расчетную длину образца lk,включающую место его разрыва, определяют следующим способом.
После испытания части образца тщательно складывают вместе, располагая их по прямой линии. От места разрыва в одну сторону откладывают половину количества интервалов в расчетной длине п/2 и ставят метку а. Если величина п/2 оказывается дробной, то ее округляют до целого числа в большую сторону. Участок от места разрыва до первой метки при этом считается как целый интервал.
От метки а откладывают в сторону разрыва п интервалов и ставят метку b (рис. 5.2, а). Отрезок ab равен конечной расчетной длине lk.Величину lk измеряют линейкой с точностью 0,5 мм.
Если место разрыва ближе к краю захвата машины, чем величина п/2(рис. 5.2, б), то полученную после разрыва конечную расчетную длину lk определяют следующим образом: от места разрыва до крайней метки q у захвата определяют число интервалов, которое обозначают т/2. От точки q к месту разрыва откладывают т интервалов и ставят метку с. Затем от метки с откладывают п/2 – m/2интервалов и ставят метку е.
Конечную расчетную длину образца lk, мм, вычисляют по формуле
lk = cq + 2ce,
где cq и се – соответственно длина участка образца между точками с и q, с и е.
Для определения величины относительного равномерного удлинения р конечная расчетная длина lи определяется по меткам на участке испытанной арматуры, на котором не произошло разрыва (см. рис. 5.2).
Рис. 5.2. Схемы измерения начальной и конечной расчетных длин:
а – разрыв в средине образца; б – разрыв около захвата
Величину относительного равномерного удлинения δp, %, вычисляют по формуле
(5.3)
Конечные расчетные длины lkи lи измеряют с погрешностью не более 0,5 мм.
Определение напряжений. Прежде чем перейти к определению напряжений на характерных уровнях нагрузки, рассмотрим более подробно диаграммы (рис. 5.3).
Рис. 5.3. Диаграммы растяжения арматуры:
а – с площадкой текучести; б – без площадки текучести
Предел текучести (физический)σT – напряжение, при котором образец деформируется без увеличения растягивающей нагрузки. Предел текучести σT, МПа (кгс/мм2), вычисляют с погрешностью не более 5 МПа (0,5 кгс/мм2) по формуле
. (5.4)
Условный предел текучести σ0,2 – напряжение, вызывающее остаточную деформацию, равную 0,2 %.
Условный предел упругости (пропорциональности) σ0,02 – напряжение, вызывающее остаточную деформацию, равную 0,02 %.
Условные пределы упругости и текучести могут быть определены аналитическим или графическим способом.
Временное сопротивление (предел прочности)σВ – напряжение, вызывающее образование шейки и разрушение образца. Временное сопротивление σВ, МПа (кгс/мм2), вычисляют с погрешностью не более 5 МПа (0,5 кгс/мм2) по формуле
(5.5)
Модуль упругостиЕ – сопротивление металла упругой деформации. Для стержней и проволоки начальный модуль упругости равен отношению приращения напряжений в интервале от 0,1 до 0,35 к относительному удлинению образца в том же интервале нагружения.
Начальный модуль упругости Ен определяют с погрешностью не более 1 % по формуле
(5.6)
При этом в интервале от 0,1 до 0,35 должно быть не менее трех последовательных этапов нагружения.
Для арматурных канатов начальный модуль упругости определяется после двукратного нагружения и разгружения в интервале 0,1 и 0,35 .
За результат испытания принимаются механические свойства, полученные при испытании каждого образца. Количество образцов для испытаний указывается в нормативно-технической документации на арматурную сталь.
Результаты испытаний не учитываются в следующих случаях:
– при разрыве образца по нанесенным меткам, если при этом какая-либо характеристика механических свойств по своей величине не отвечает установленным требованиям;
– при разрыве образца в захватах испытательной машины;
– при обнаружении ошибок в проведении испытаний или записи результатов испытаний.
Дата добавления: 2014-11-25; Просмотров: 4723; Нарушение авторских прав?
Нам важно ваше мнение! Был ли полезен опубликованный материал? Да | Нет
Рекомендуемые страницы:
Источник
Испытание арматуры на растяжение и прочность
Проводим испытания на относительное удлинение и сужение после разрыва, временное сопротивление, оцениваем предел текучести и упругости
Стоимость испытаний механических свойств арматуры
9. Арматура. Механические свойства | ||||
9.1 | Механические испытания арматурной стали на растяжение и изгиб (диаметр до 25 мм, включительно) | ГОСТ 12004-81 | 1 образец | 2 500 |
9.2 | Механические испытания арматурной стали на растяжение и изгиб (диаметр от 28 мм, включительно) | ГОСТ 12004-81 | 1 образец | 3 500 |
9.3 | Механические испытания сварного шва арматурной стали на растяжение (диаметр до 28 мм, включительно) | ГОСТ 12004-81 | 1 образец | 3 000 |
9.4 | Механические испытания сварного шва арматурной стали на растяжение (диаметр от 28 мм, включительно) | ГОСТ 12004-81 | 1 образец | 4 000 |
9.5 | Механические испытания муфтовых соединений арматурной стали, на растяжение (диаметр до 28 мм, включительно) | ГОСТ 12004-81 | 1 образец | 5 000 |
9.6 | Механические испытания муфтовых соединений арматурной стали, на растяжение (диаметр от 28 мм, включительно) | ГОСТ 12004-81 | 1 образец | 6 500 |
9.7 | Визуально-измерительный контроль арматурных каркасов | РД 03-606-03 | 1 образец | от 2000 |
Испытание арматуры – это необходимая процедура, которая проводится для контроля соответствия техническим нормам ГОСТ при возведении коммерческих, жилых или промышленных зданий. Среди основных контролируемых и изучаемых параметров выделяют следующие:
- Предел прочности;
- Напряжение, соответствующее нормам;
- Испытание растяжения;
- Габариты, предел текучести;
- Относительное удлинение.
Такие испытания проводятся в профессиональной лаборатории с использованием точной измерительной аппаратуры и стендов. Полученные данные сверяются с установленным государственным стандартом, после чего заказчик получает развернутый анализ, отображающий информацию о допуске или не допуске использования той или иной партии металлических заготовок для строительства. Работы ведутся не только с образцами, но и готовыми конструкциями методом неразрушающего контроля.
Общие условия исследований позволяют установить качество стали, прочность сварных соединений, плотность. Если образцы не соответствуют условиям, то в течение нескольких лет цельность железобетонных конструкций в возведенных зданиях может нарушиться (именно для ЖБИ чаще всего и используется арматура).
Какие методы контроля качества используются в лаборатории
Первичная процедура – это комплексный замер габаритов взятых образцов. Определяется длина образца, сечение образца, диаметр. Все проверки соответствуют государственным нормам (например, измерение прочности арматуры на растяжение осуществляется по ГОСТ 1497). Для таких процедур используются специальные стенды, создающие определенную нагрузку на заготовку. Измерение силы давления отображается в последствии на графике. Дополнительно может анализироваться качество стали и возможность эксплуатации металлических заготовок в условиях повышенной температуры, в пожароопасной среде или в близости к химическим реагентам.
Для точного внутреннего изучения плотности применяются методы неразрушающего контроля (рентгеновские аппараты, ультразвуковое и электромагнитное оборудование). С их помощью устанавливается не только качество сварных соединений, но и могут быть замечены внутренние дефекты, образованные во время проката стали. Такие параметры, как качество поперечного сечения устанавливаются визуальным осмотром специалиста.
Общее время проведения лабораторных исследований составляет не более трех-четырех рабочих дней, в зависимости от типа арматуры и других условий. Лаборатория оборудована всеми необходимыми устройствами, стендами и аппаратурой для качественных изучений. Заказчику по результату проверки выдается письменный бланк с полученными данными в виде цифровых значений, графических кривых и общего вывода относительно рациональности использования той или иной партии арматуры для строительных работ.
Источник
Наряду с классической стальной арматурой, в строительстве все чаще применяют полимерную композитную арматуру, и для обоих видов этой продукции проводят испытания. Контролю подлежат геометрические параметры и физико-механические характеристики.
Проведение испытаний металлической арматуры
Арматурные изделия, применяемые для усиления железобетонных конструкций, выпускают в соответствии с ГОСТом 5781-82. Согласно нормативному документу, эта продукция по физико-механическим характеристикам подразделяется на классы от A-I до A-VI. Изделия класса A-I имеют гладкую поверхность, остальных – гладкую или периодического профиля.
ГОСТ 5781-82 подразумевает проведение ряда испытаний арматуры.
Определение диаметра
Для определения этого размера у гладкой арматуры используют штангенциркуль. Диаметр продукции с периодическим профилем находят с использованием формул.
Сначала вычисляют площадь поперечного сечения:
S = m/pxl, где:
S – площадь поперечного сечения, м2;
m – масса образца, кг;
p – плотность, равная 7850 кг/м3(это средняя величина, для конкретной марки можно подставить точное значение);
l – длина образца, м.
Диаметр вычисляют по формуле:
D = √4S/π, где:
D –диаметр стержня, м;
S – площадь сечения, м2.
Для практических целей диаметр изделий периодического профиля вычисляют как среднюю величину диаметров по ребрам или между ними.
Класс арматуры: определяется по результатам испытаний на растяжение
Образцы должны иметь необработанную поверхность номинальным диаметром 3,0-80,0 мм, длина зависит от рабочей длины и конструкционных особенностей захвата оборудования, на котором производятся исследования.
Нормируемые характеристики при испытаниях на растяжение:
- предел текучести (физический) – это напряжение, при котором образец претерпевает деформационные изменения без роста растягивающей нагрузки;
- предел текучести условный – напряжение, при котором величина остаточной деформации составляет 0,2%;
- временное сопротивление разрыву – предел прочности, испытания на него позволяют определить величину, при которой появляется шейка и разрушения испытуемого изделия;
- относительное удлинение – равно соотношению разности конечной и начальной расчетных длин к начальной длине.
Методы испытаний стеклопластиковой и другой композитной полимерной арматуры
Композитная арматура представляет собой продукцию, состоящую из:
- стержня – скопления продольно ориентированных нитей;
- обмоточного жгута – скопления нитей, ориентированных винтообразно;
- матрицы – термореактивной смолы из нескольких жидких компонентов, переведенных в твердую фазу.
Испытания на соответствие изделий ГОСТу 31938-2012 включают определение:
- геометрических параметров – номинального и внешнего диаметров, длины;
- механических свойств при осевом растяжении – модуля упругости, предела прочности, относительного удлинения;
- предела прочности при сжатии;
- предела прочности при срезе стержня поперек расположения волокон;
- предела прочности сцепления с бетоном – испытанием балки на изгибающие нагрузки или осевым выдергиванием из куба;
- устойчивости к щелочным средам – это испытание длится в течение 30 суток при температуре +60°C;
- максимальной эксплуатационной температуры;
- удельной эффективной активности радионуклидов сырья.
Каждое исследование производится минимум на шести образцах.
Источник