Что связывает модуль упругости при растяжении
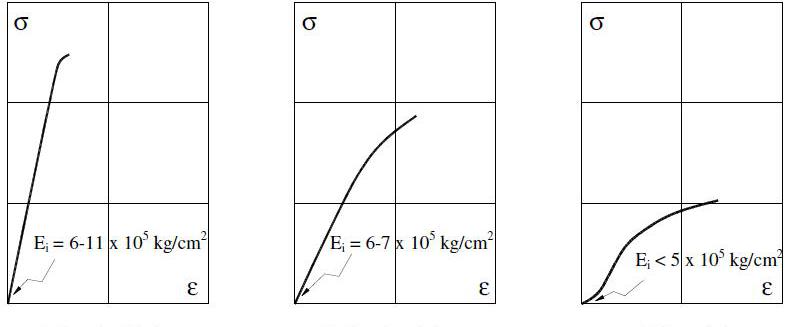
Все твердые тела, как кристаллические, так и аморфные, имеют свойство изменять свою форму под воздействие приложенной к ним силы. Другими словами, они подвергаются деформации. Если тело возвращается к исходным размерам и форме после того, как внешнее усилие прекращает свое воздействие, то его называют упругим, а его деформацию считают упругой. Для любого тела существует предел приложенного усилия, после которого деформация перестает быть упругой, тело не возвращается в исходную форму и к исходным размерам, а остается в деформированном состоянии или разрушается. Теория упругих деформаций тел была создана в конце 17 века британским ученым Р. Гуком и развита в трудах его соотечественника Томаса Юнга. В их честь Гука и Юнга были названы соответственно закон и коэффициент, определяющий степень упругости тел. Он активно применяется в инженерном деле в ходе расчетов прочности конструкций и изделий.
Модуль Юнга
Основные сведения
Модуль Юнга, (называемый также модулем продольной упругости и модулем упругости первого рода) это важная механическая характеристика вещества. Он является мерой сопротивляемости продольным деформациям и определяет степень жесткости. Он обозначается как E; измеряется н/м2 или в Па.
Это важный коэффициент применяют при расчетах жесткости заготовок, узлов и конструкций, в определении их устойчивости к продольным деформациям. Вещества, применяемые для изготовления промышленных и строительных конструкций, имеют, как правило, весьма большие значения E. И поэтому на практике значения Е для них приводят в гигаПаскалях (1012Па)
Величину E для стержней поддается расчету, у более сложных конструкций она измеряется в ходе опытов.
Приближенные величины E возможно узнать из графика, построенного в ходе тестов на растяжение.
График теста на растяжение
E- это частное от деления нормальных напряжений σ на относительное удлинение ε.
E=α/ε
Закон Гука также можно сформулировать и с использованием модуля Юнга.
Физический смысл модуля Юнга
Во время принудительного изменения формы предметов внутри них порождаются силы, сопротивляющиеся такому изменению, и стремящиеся к восстановлению исходной формы и размеров упругих тел.
Если же тело не оказывает сопротивления изменению формы и по окончании воздействия остается в деформированном виде, то такое тело называют абсолютно неупругим, или пластичным. Характерным примером пластичного тела является брусок пластилина.
Виды деформации
Р. Гук исследовал удлинение стрежней из различных веществ, под воздействием подвешенных к свободному концу гирь. Количественным выражением степени изменения формы считают относительное удлинение, равное отношению абсолютного удлинения и исходной длины.
В результате серии опытов было установлено, что абсолютное удлинение пропорционально с коэффициентом упругости исходной длине стрежня и деформирующей силе F и обратно пропорционально площади сечения этого стержня S:
Δl = α * (lF) / S
Величину, обратную α, и называют модулем Юнга:
1/α = E
Относительная деформация:
ε = (Δl) / l = α * (F/S)
Отношение растягивающей силы F к S называют упругим напряжением σ:
ε=α σ
Закон Гука, записанный с использованием модуля Юнга, выглядит так:
σ = ε/α = E ε
Теперь можно сформулировать физический смысл модуля Юнга: он соответствует напряжению, вызываемому растягиванием стержнеобразного образца вдвое, при условии сохранения целостности.
В реальности подавляющее большинство образцов разрушаются до того, как растянутся вдвое от первоначальной длины. Значение E вычисляют с помощью косвенного метода на малых деформациях.
Коэффициент жёсткости при упругой деформации стержня вдоль его оси k = (ES) / l
Модуль Юнга определяет величину потенциальной энергии тел или сред, подвергшихся упругой деформации.
Значения модуля юнга для некоторых материалов
В таблице показаны значения E ряда распространенных веществ.
Материал | модуль Юнга E, ГПа |
Алюминий | 70 |
Бронза | 75-125 |
Вольфрам | 350 |
Графен | 1000 |
Латунь | 95 |
Лёд | 3 |
Медь | 110 |
Свинец | 18 |
Серебро | 80 |
Серый чугун | 110 |
Сталь | 200/210 |
Стекло | 70 |
Модуль продольной упругости стали вдвое больше модуля Юнга меди или чугуна. Модуль Юнга широко применяется в формулах прочностных расчетов элементов конструкций и изделий в целом.
Предел прочности материала
Это предел возникающего напряжения, после которого образец начинает разрушаться.
Статический предел прочности измеряется при продолжительном приложении деформирующего усилия, динамический — при кратковременном, ударном характере такого усилия. Для большинства веществ динамический предел больше, чем статический.
Инструмент для определения предела прочности
Кроме того, существуют пределы прочности на сжатие материала и на растяжение. Они определяются на испытательных стенда опытным путем, при растягивании или сжатии образцов мощными гидравлическим машинами, снабженными точными динамометрами и измерителями давления. В случае невозможности достижения требуемого давления гидравлическим способом иногда применяют направленный взрыв в герметичной капсуле.
Допускаемое механическое напряжение в некоторых материалах при растяжении
Из жизненного опыта известно, что разные материалы по-разному сопротивляются изменению формы. Прочностные характеристики кристаллических и других твердых тел определяются силами межатомного взаимодействия. По мере роста межатомных расстояний возрастают и силы, притягивающие атомы друг к другу. Эти силы достигают максимума при определенной величине напряжения, равной приблизительно одной десятой от модуля Юнга.
Испытание на растяжение
Эту величину называют теоретической прочностью, при ее превышении начинается разрушение материала. В реальности разрушение начинается при меньших значениях, поскольку строение реальных образцов неоднородно. Это вызывает неравномерное распределение напряжений, и разрушение начинается с тех участков, где напряжения максимальны.
Значения σраст в МПа:
Материалы | σраст | |
Бор | 5700 | 0,083 |
Графит | 2390 | 0,023 |
Сапфир | 1495 | 0,030 |
Стальная проволока | 415 | 0,01 |
Стекловолокно | 350 | 0,034 |
Конструкционная сталь | 60 | 0,003 |
Нейлон | 48 | 0,0025 |
Эти цифры учитываются конструкторами при выборе материала деталей будущего изделия. С их использованием также проводятся прочностные расчеты. Так, например, тросы, используемые для подъемно- транспортных работ, должны иметь десятикратный запас по прочности. Периодически их проверяют, подвешивая груз в десять раз больше, чем паспортная грузоподъемность троса.
Запасы прочности, закладываемые в ответственные конструкции, также многократны.
Коэффициент запаса прочности
Для количественного выражения запаса прочности при конструировании применяют коэффициент запаса прочности. Он характеризует способность изделия к перегрузкам выше номинальных. Для бытовых изделий он невелик, но для ответственных узлов и деталей, могущих при разрушении представлять опасность для жизни и здоровья человека, его делают многократным.
Запас прочности
Точный расчет прочностных характеристик позволяет создать достаточный для безопасности запас прочности и одновременно не перетяжелить конструкцию, ухудшая ее эксплуатационные характеристики. Для таких расчетов используются сложные математические методы и совершенное программное обеспечение. Наиболее важные конструкции обсчитывают на суперкомпьютерах.
Связь с другими модулями упругости
Модуль Юнга связан с модулем сдвига, определяющим способность образца к сопротивлению против деформации сдвига, следующим соотношением:
E связан также и с модулем объёмной упругости, определяющим способность образца к сопротивлению против одновременного сжатия со всех сторон.
Источник
Модуль упругости — это физическая величина, которая характеризует упругое поведение материала при приложении к нему внешней силы в конкретном направлении. Под упругим поведением материала подразумевается его деформация в упругой области.
История исследования упругости материалов
Физическая теория упругих тел и их поведения при действии внешних сил была подробно рассмотрена и изучена английским ученым XIX века Томасом Юнгом. Однако сама концепция упругости была развита еще в 1727 году швейцарским математиком, физиком и философом Леонардом Эйлером, а первые эксперименты, связанные с модулем упругости, провел в 1782 году, то есть за 25 лет до работ Томаса Юнга, венецианский математик и философ Якопо Рикатти.
Заслуга Томаса Юнга заключается в том, что он придал теории упругости стройный современный вид, который впоследствии был оформлен в виде простого, а затем и обобщенного закона Гука.
Физическая природа упругости
Любое тело состоит из атомов, между которыми действуют силы притяжения и отталкивания. Равновесие этих сил обуславливает состояние и параметры вещества при данных условиях. Атомы твердого тела при приложении к ним незначительных внешних сил растяжения или сжатия начинают смещаться, создавая противоположную по направлению и равную по модулю силу, которая стремится вернуть атомы в начальное состояние.
В процессе такого смещения атомов энергия всей системы увеличивается. Эксперименты показывают, что при малых деформациях энергия пропорциональна квадрату величины этих деформаций. Это означает, что сила, будучи производной по энергии, оказывается пропорциональной первой степени величины деформации, то есть зависит от нее линейно. Отвечая на вопрос, что такое модуль упругости, можно сказать, что это коэффициент пропорциональности между силой, действующей на атом, и деформацией, которую эта сила вызывает. Размерность модуля Юнга совпадает с размерностью давления (Паскаль).
Предел упругости
Согласно определению, модуль упругости показывает, какое напряжение нужно приложить к твердому телу, чтобы его деформация составила 100 %. Однако все твердые тела обладают пределом упругости, который равен 1 % деформации. Это означает, что если приложить соответствующее усилие и деформировать тело на величину, меньшую 1 %, тогда после прекращения действия этого усилия тело точно восстанавливает свою первоначальную форму и размеры. При приложении слишком большого усилия, при котором величина деформации превышает 1 %, после прекращения действия внешней силы тело уже не восстановит первоначальные размеры. В последнем случае говорят о существовании остаточной деформации, которая является свидетельством превышения упругого предела данного материала.
Модуль Юнга в действии
Для определения модуля упругости, а также для понимания, как им пользоваться, можно привести простой пример с пружиной. Для этого необходимо взять металлическую пружину и измерить площадь круга, который образуют ее витки. Это делается по простой формуле S = πr², где п — число пи, равное 3,14, а r — радиус витка пружины.
Далее следует замерить длину пружины l0 без нагрузки. Если повесить какой-либо груз массой m1 на пружину, тогда она увеличит свою длину до некоторой величины l1. Модуль упругости E можно вычислить, исходя из знания закона Гука по формуле: E = m1gl0/(S(l1-l0)), где g — ускорение свободного падения. В данном случае отметим, что величина деформации пружины в упругой области может намного превышать 1 %.
Знание модуля Юнга позволяет предсказывать величину деформации при действии конкретного напряжения. В данном случае, если повесить на пружину другую массу m2, получим следующую величину относительной деформации: d = m2g/(SE), где d — относительная деформация в упругой области.
Изотропия и анизотропия
Модуль упругости является характеристикой материала, которая описывает силу связи между его атомами и молекулами, однако конкретный материал может иметь несколько различных модулей Юнга.
Дело в том, что свойства каждого твердого тела зависят от его внутренней структуры. Если свойства одинаковы во всех пространственных направлениях, то речь идет об изотропном материале. Такие вещества имеют однородное строение, поэтому действие внешней силы в различных направлениях на них вызывает одинаковую реакцию со стороны материала. Все аморфные материалы обладают изотропией, например, резина или стекло.
Анизотропия — явление, которое характеризуется зависимостью физических свойств твердого тела или жидкости от направления. Все металлы и сплавы на их основе обладают той или иной кристаллической решеткой, то есть упорядоченным, а не хаотичным расположением ионных остовов. Для таких материалов модуль упругости меняется в зависимости от оси действия внешнего напряжения. Например, металлы с кубической симметрией, к которым относятся алюминий, медь, серебро, тугоплавкие металлы и другие, обладают тремя различными модулями Юнга.
Модуль сдвига
Описание упругих свойств даже изотропного материала не обходится знанием одного модуля Юнга. Поскольку, помимо растяжения и сжатия, на материал можно подействовать сдвиговыми напряжениями или напряжениями кручения. В этом случае он будет реагировать на внешнее усилие иначе. Для описания упругой деформации сдвига вводят аналог модуля Юнга, модуль сдвига или модуль упругости второго рода.
Все материалы слабее сопротивляются сдвиговым напряжениям, чем растяжению или сжатию, поэтому значение модуля сдвига для них в 2-3 раза меньше, чем значения модуля Юнга. Так, для титана, модуль Юнга которого равен 107 ГПа, модуль сдвига составляет всего лишь 40 ГПа, для стали эти цифры имеют значения 210 ГПа и 80 ГПа, соответственно.
Модуль упругости дерева
Дерево относится к анизотропным материалам, поскольку древесные волокна ориентированы вдоль конкретного направления. Именно вдоль волокон измеряют модуль упругости древесины, поскольку поперек волокон он меньше на 1-2 порядка. Знание модуля Юнга для дерева играет важную роль и учитывается при проектировании конструкций из деревянных панелей.
Значения модуля упругости древесины для некоторых видов деревьев приведены в таблице ниже.
Вид дерева | Модуль Юнга в ГПа |
Лавровое дерево | 14 |
Эвкалипт | 18 |
Кедр | 8 |
Ель | 11 |
Сосна | 10 |
Дуб | 12 |
Следует отметить, что приведенные значения могут отличаться на величину порядка 1 ГПа для конкретного дерева, поскольку на его модуль Юнга влияет плотность древесины и условия произрастания.
Модули сдвига для различных пород деревьев находятся в пределах 1-2 ГПа, например, для сосны это 1,21 ГПа, а для дуба 1,38 ГПа, то есть древесина практически не сопротивляется сдвиговым напряжениям. Данный факт должен учитываться при изготовлении деревянных несущих конструкций, которые проектируют так, чтобы они работали только на растяжение или сжатие.
Характеристики упругости металлов
Если сравнивать с модулем Юнга древесины, то средние значения этой величины для металлов и сплавов на порядок больше, что показано в следующей таблице.
Металл | Модуль Юнга в ГПа |
Бронза | 120 |
Медь | 110 |
Сталь | 210 |
Титан | 107 |
Никель | 204 |
Упругие свойства металлов, которые имеют кубическую сингонию, описываются тремя упругими постоянными. К таким металлам относятся медь, никель, алюминий, железо. Если металл имеет гексагональную сингонию, тогда для описания его упругих характеристик уже необходимо шесть постоянных.
Для металлических систем модуль Юнга измеряют в пределах 0,2 % деформации, поскольку большие значения могут происходить уже в неупругой области.
Источник
Дата введения 1982-07-01
Постановлением государственного комитета СССР по стандартам от 26 августа 1981 г. N 4058 дата введения установлена 01.07.82
Ограничение срока действия снято по протоколу N 5-94 Межгосударственного совета по стандартизации, метрологии и сертификации (ИУС 11-12-94)
ВЗАМЕН ГОСТ 9550-71
ИЗДАНИЕ (май 2004 г.) с Поправкой (ИУС 11-89).
Настоящий стандарт распространяется на пластмассы и устанавливает методы определения модуля упругости при растяжении, сжатии и изгибе.
Стандарт не распространяется на ячеистые пластмассы и пленки из пластмасс.
Стандарт полностью соответствует СТ СЭВ 2345-80.
Термины, применяемые в настоящем стандарте, и их пояснения приведены в приложении.
1. МЕТОД ОПРЕДЕЛЕНИЯ МОДУЛЯ УПРУГОСТИ ПРИ РАСТЯЖЕНИИ
1.1. Сущность метода
Сущность метода заключается в определении модуля упругости при растяжении как отношения приращения напряжения к соответствующему приращению относительного удлинения, установленному настоящим стандартом.
1.2. Отбор образцов
1.2.1. Для испытания применяют образцы по ГОСТ 11262-80.
1.2.2. Количество образцов, взятых для испытания одной партии материала, а для анизотропных материалов в каждом из выбранных направлений, должно быть не менее 3.
1.3. Аппаратура
Для проведения испытания применяют аппаратуру по ГОСТ 11262-80, при этом испытательная машина должна обеспечивать скорость раздвижения зажимов (1,0±0,5)% в минуту, а прибор для измерения удлинения должен обеспечивать измерение с погрешностью не более 0,002 мм.
1.4. Подготовка к испытанию
1.4.1. Перед испытанием образцы кондиционируют в стандартной атмосфере по ГОСТ 12423-66 не менее 16 ч, если в нормативно-технической документации на конкретную продукцию нет других указаний.
1.4.2. Перед испытанием измеряют толщину и ширину образца по ГОСТ 11262-80.
1.5. Проведение испытания
1.5.1. Испытание проводят при температуре и относительной влажности, указанных в нормативно-технической документации на конкретную продукцию.
Если в нормативно-технической документации на конкретную продукцию нет других указаний, то испытание проводят в соответствии с ГОСТ 12423-66 при температуре (23±2) °С и относительной влажности (50±5)%.
1.5.2. Образец закрепляют в машину так, чтобы продольные оси зажимов и ось образца совпадали с линией, соединяющей точки крепления зажимов на испытательной машине.
1.5.3. На образце, закрепленном в зажимах, проводят установку и настройку прибора для измерения удлинения.
1.5.4. Образец нагружают при скорости раздвижения зажимов испытательной машины, обеспечивающей скорость деформации образца (1,0±0,5)% в минуту. Нагружение осуществляют до величины относительного удлинения 0,5%.
Если образцы разрушаются до достижения относительного удлинения 0,5%, нагружение проводят до меньшей величины деформации, установленной в нормативно-технической документации на конкретную продукцию.
1.5.5. Графическую запись нагрузки и деформации проводят в следующем масштабе:
100-150 мм на диаграмме должно соответствовать 0,4% относительного удлинения;
не менее 100 мм на диаграмме должно соответствовать приращению нагрузки, соответствующему увеличению относительного удлинения на 0,4%.
1.6. Обработка результатов
1.6.1. По диаграмме определяют значения нагрузки, соответствующие величинам относительного удлинения 0,1 и 0,3%. Допускаются меньшие значения относительного удлинения для образцов, предусмотренных в п.1.5.4.
1.6.2. Модуль упругости при растяжении () в МПа вычисляют по формуле
,
где — нагрузка, соответствующая относительному удлинению 0,3%, Н;
— нагрузка, соответствующая относительному удлинению 0,1%, Н;
— расчетная длина образца, мм;
— площадь начального поперечного сечения образца, мм;
— удлинение, соответствующее нагрузке , мм;
— удлинение, соответствующее нагрузке ,
мм.
1.6.3. За результат испытания принимают среднеарифметическое значение всех параллельных определений.
1.6.4. Величину стандартного отклонения вычисляют по ГОСТ 14359-69.
1.6.5. Результаты испытания записывают в протокол, который должен содержать следующие данные:
наименование и марку пластмассы и номер партии;
метод испытания;
наименование испытательной машины;
тип и марку прибора для измерения деформации;
условия проведения испытания (скорость нагружения, температура, графическая запись и т.д.);
тип испытуемого образца (форма, размеры);
условия подготовки испытуемого образца;
количество образцов, взятых для испытания;
среднеарифметическое определяемого показателя и стандартное отклонение;
дату испытания;
обозначение настоящего стандарта.
2. МЕТОД ОПРЕДЕЛЕНИЯ МОДУЛЯ УПРУГОСТИ ПРИ СЖАТИИ
2.1. Сущность метода
Сущность метода заключается в определении модуля упругости при сжатии как отношения приращения напряжения к соответствующему приращению относительной деформации сжатия, установленному настоящим стандартом.
2.2. Отбор образцов
2.2.1. Для испытания применяют образцы по ГОСТ 4651-82. База измерения деформации должна составлять не менее 10 мм и не более высоты образца при измерении деформации прибором, установленным на образце.
При изготовлении образцов из изделий толщиной менее 5 мм используют образцы в форме прямоугольных пластин размерами (80±2)х(10,0±0,5) мм, а толщина образца равна толщине изделия. Для армированных пластмасс ширина образцов равна (15,0±0,5) мм. Для предотвращения потери устойчивости при испытании таких образцов применяют приспособление (черт.1).
Черт.1. Приспособление для испытания на сжатие образцов толщиной менее 5 мм
Приспособление для испытания на сжатие образцов толщиной менее 5 мм
Черт.1
2.2.2. Количество образцов должно соответствовать п.1.2.2.
2.3. Аппаратура
Для проведения испытания применяют аппаратуру по ГОСТ 4651-82, при этом испытательная машина должна обеспечивать скорость сближения опорных площадок со скоростью деформации образца (1,0±0,5)% в минуту, а прибор для измерения деформации сжатия должен обеспечивать измерение с погрешностью не более 0,002 мм.
2.4. Подготовка к испытанию
2.4.1. Перед испытанием образцы кондиционируют в стандартной атмосфере по ГОСТ 12423-66 не менее 16 ч, если в нормативно-технической документации на конфетную продукцию нет других указаний.
2.4.2. Перед испытанием измеряют размеры образцов по ГОСТ 4651-82.
2.5. Проведение испытания
2.5.1. Испытания проводят при температуре и относительной влажности, указанных в п.1.5.1.
2.5.2. Образец устанавливают на опорных плитах испытательной машины так, чтобы продольная ось образца совпадала с направлением действия силы.
2.5.3. Устанавливают прибор для измерения деформации. Деформацию при сжатии определяют измерением расстояния между площадками или по изменению базы на образце (см. п.2.2.1).
2.5.4. Образец нагружают при скорости сближения площадок испытательной машины, обеспечивающей скорость деформации образца (1,0±0,5)% в минуту. Нагружение осуществляют до величины деформации 0,5%.
Если образцы разрушаются до достижения относительной деформации 0,5%, нагружение осуществляют до меньшей величины деформации, установленной в нормативно-технической документации на конкретную продукцию.
2.5.5. Графическую запись нагрузки и деформации проводят в соответствии с п.1.5.5 при значениях относительной деформации сжатия, равных значениям относительного удлинения, указанных в п.1.5.5.
2.6. Обработка результатов
2.6.1. По диаграмме определяют значения нагрузки, соответствующие величинам относительной деформации 0,1 и 0,3%.
Допускаются меньшие значения относительной деформации при сжатии для образцов, предусмотренных в п.2.5.4.
2.6.2. Модуль упругости при сжатии () в МПа вычисляют по формуле
,
где — нагрузка, соответствующая относительной деформации 0,3%, Н;
— нагрузка, соответствующая относительной деформации 0,1%, Н;
— начальная высота образца или базы, мм;
— площадь начального поперечного сечения образца, мм;
— изменение высоты или базы, соответствующее нагрузке , мм;
— изменение высоты или базы, соответствующее нагрузке, ,
мм.
2.6.3. За результат испытания принимают среднеарифметическое значение всех параллельных определений.
2.6.4. Величину стандартного отклонения вычисляют, как указано в п.1.6.4.
2.6.5. Результаты испытания оформляют протоколом, как указано в п.1.6.5.
3. МЕТОД ОПРЕДЕЛЕНИЯ МОДУЛЯ УПРУГОСТИ ПРИ ИЗГИБЕ
3.1. Сущность метода
Сущность метода заключается в определении модуля упругости при изгибе как отношения приращения напряжения к соответствующему приращению относительной деформации, установленному настоящим стандартом.
3.2. Отбор образцов
3.2.1. Для испытания применяют образцы по ГОСТ 4648-71.
3.2.2. Количество образцов должно соответствовать п.1.2.2.
3.3. Аппаратура
Для проведения испытания применяют аппаратуру по ГОСТ 4648-71, при этом испытательная машина должна обеспечивать скорость сближения нагружающего наконечника и опор, соответствующую скорости деформации образца (1,0±0,5)% в минуту, а прибор для измерения деформации образца должен обеспечивать измерение с погрешностью не более 0,01 мм.
3.4. Подготовка к испытанию
3.4.1. Перед испытанием образцы кондиционируют в стандартной атмосфере по ГОСТ 12423-66 не менее 16 ч, если в нормативно-технической документации на конкретную продукцию нет других указаний.
3.4.2. Перед испытанием измеряют размеры образцов по ГОСТ 4648-71.
3.5. Проведение испытания
3.5.1. Испытания на изгиб проводят двумя методами:
А — при нагружении по трехточечной схеме (черт.2);
Б — при нагружении по четырехточечной схеме (черт.3).
Черт.2. Трехточечная схема нагружения при изгибе
Трехточечная схема нагружения при изгибе
Метод А
Черт.2
Черт.3. Четырехточечная схема нагружения при изгибе
Четырехточечная схема нагружения при изгибе
Метод Б
— нагрузка; — расстояние между опорами; — прогиб; — эпюра момента
Черт.3
При методе А испытуемый образец нагружают наконечником в середине расстояния между опорами.
При методе Б испытуемый образец нагружают парой наконечников, расположенных в средней трети расстояния между опорами.
Выбор метода предусматривается в нормативно-технической документации на конкретную продукцию.
Прогиб измеряют:
в методе А — в середине расстояния между опорами (черт.2). Величину прогиба оценивают по величине перемещения подвижной части нагружающего устройства;
в методе Б — в соответствии с черт.3.
3.5.2. Испытания проводят при температуре и относительной влажности, указанных в п.1.5.1.
3.5.3. Расстояние между опорами () устанавливают в зависимости от толщины образца () от 15 до 17 мм и измеряют с погрешностью не более 0,5%.
3.5.4. На образце, лежащем на опорах, осуществляют установку и настройку прибора для измерения прогиба.
3.5.5. Образцы нагружают при скорости сближения нагружающего наконечника и опор, обеспечивающей скорость деформации образца (1,0±0,5)% в минуту.
Нагружение осуществляют до величины относительной деформации крайних волокон 0,5%.
Относительную деформацию крайних волокон () вычисляют по формуле
для метода А
;
для метода Б
,
где — значение прогиба, мм;
— толщина образца, мм;
— расстояние между опорами, мм.
Если образцы разрушаются до достижения относительной деформации крайних волокон 0,5%, нагружение осуществляют до меньшей величины деформации, установленной в нормативно-технической документации на конкретную продукцию.
3.5.6. Графическую запись нагрузки и деформации проводят в соответствии с п.1.5.5 при значениях прогиба, соответствующих значениям относительной деформации крайних волокон, указанных в п.1.5.5.
3.6. Обработка результатов
3.6.1. По диаграмме определяют значения нагрузки и прогиба, соответствующие значениям относительной деформации крайних волокон 0,1 и 0,3%.
Допускаются меньшие значения относительной деформации при изгибе для образцов, предусмотренных в п.3.5.5.
3.6.2. Модуль упругости при изгибе () в МПа вычисляют по формуле
для метода А
;
для метода Б
,
где — расстояние между опорами, мм;
— нагрузка при величине относительной деформации крайних волокон 0,3%, Н;
— нагрузка при величине относительной деформации крайних волокон 0,1%, Н;
— ширина образца, мм;
— толщина образца, мм;
— прогиб образца, соответствующий относительной деформации крайних волокон 0,3%, мм;
— прогиб образца, соответствующий относительной деформации крайних волокон 0,1%, мм
.
3.6.3. За результат испытания принимают среднеарифметическое значение всех параллельных определений.
3.6.4. Величину стандартного отклонения вычисляют, как указано в п.1.6.4.
3.6.5. Результаты испытания оформляют протоколом, как указано в п.1.6.5.
ПРИЛОЖЕНИЕ (справочное). Термины, применяемые в настоящем стандарте, и их пояснения
ПРИЛОЖЕНИЕ
Справочное
Понятие | Обозначение | Единица измерения | Определение |
Модуль упругости | МПа | Мера жесткости материала, характеризующаяся сопротивлением развитию упругих деформаций. | |
при растяжении | МПа | Модуль упругости определяют как отношение приращения напряжения к соответствующему приращению деформации | |
при сжатии | МПа | ||
при изгибе | МПа | ||
2. Скорость деформации | мин | Изменение относительной деформации растяжения или сжатия в единицу времени. Скорость деформации при растяжении и сжатии определяют как отношение скорости перемещения подвижного элемента испытательной машины () к длине образца между кромками зажимов или сжимающими площадками. При изгибе вычисляют по формуле для метода А ; для метода Б , где — скорость относительной деформации крайних волокон образца, равная 0,01 мин; — расстояние между опорами, мм; — толщина образца, мм. |
ПРИЛОЖЕНИЕ. (Поправка).
Текст документа сверен по:
официальное издание
М.: ИПК Издательство стандартов, 2004
Источник