Расчет проушины на растяжение
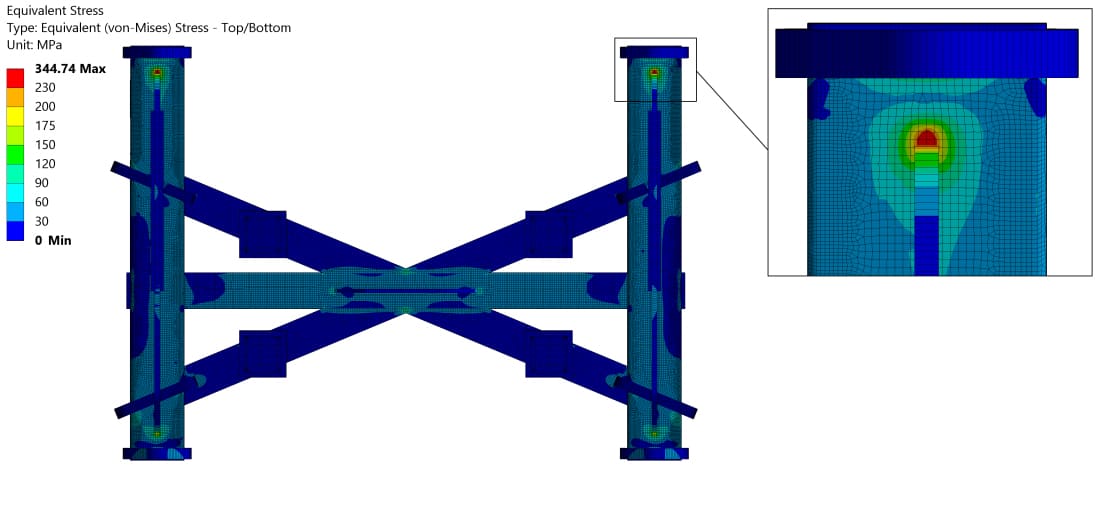
6.1. Расчет проушины на растяжение
В
опасном сечении проушины 2-2,
рис.1, развиваются напряжения растяжения,
σp
, МПа:
(10)
где
[σp]
— допускаемые напряжения при растяжении
по формуле (6) для материала проушины.
При
расчете предельных напряжений σlimпоформ.
(6):
—
коэффициент Kσpопределяют
по табл. 3 в зависимости от диаметра
отверстия d;
—
коэффициент
Kσп
определяют по табл. 4, полагая поверхность
проушины подвергнутой грубой обработке
(обдирке);
—
коэффициент Kσк
= 1 принимают как для конструкции без
концентраторов напряжений;
—
коэффициент Ку
=
1, обычно рекомендуется использовать
термическое улучшение без поверхностного
упрочнения.
Для
проектировочного расчета проушины
задают соотношение размеров:
Тогда
по формуле (10) диаметр Dи
толщина Sпроушины
равны:
(11)
Полученное
размеры округляют до больших стандартных
значений из ряда, указанного в разд. 3.
6.2. Расчет проушины по Ляме
Проверка
напряжений по Ляме актуальна для
относительно широких проушин: D/d
> 1,5.
Напряжения σл,
МПа, проверяют в опасном сечении 2-2
проушин, рис.1:
(12)
При
расчете по формуле (11) принимают
допустимые напряжения
[σл]
= (1,4…1,7)[σp].
Если
проверка по формуле (12) не обеспечена,
следует увеличить толщину проушины 2.
При
отношении D/d
< 1,5
прочность проушины по Ляме обычно
обеспечивается, если выполнена проверка
прочности на растяжение по
формулам
(10), (11).
6.3. Расчет проушины на смятие
Напряжения
смятия σсм
, МПа, между пальцем и проушиной:
(13)
где
Кнер=
4/π
– коэффициент неравномерности
распределения напряжений смятия.
При
расчёте по формуле (13) принимают
допускаемые напряжения
[σсм]=
σT
/[Sсм],
где
σT
— предел текучести материала проушины
по табл. 1;
[Sсм]
–
запас прочности, принимают [Sсм]=
1,5.
Если
условие прочности по формуле (13) не
выполнено, толщину проушины следует
увеличить. Окончательное решение о
величине толщины δ
принимают с учётом конструкции осевого
крепления пальца, см п. 7.1.
7. Указания к проектированию вариантов задания
7.1. Общие для всех вариантов указания
Фиксация
пальца в осевом направлении может быть
выполнена с помощью закладной планки,
закрепляемой на щеке обоймы с помощью
двух винтов диаметром М6…М8, (Прил. 1,2).
В этих вариантах на выступающей из
проушины концевой части пальца должен
быть выполнен паз (Прил. 1 и 2, палец
неподвижен). Глубина паза (или проточки)
h
= 3…5 мм. Толщина закладной планки t
=3…5 мм. Толщина щек проушины, найденная
в п.6.3 по условиям ее прочности, может
быть увеличена до δ
≥6..
.8 мм для размещения резьбовых гнезд
крепежных винтов.
Подвод
консистентной смазки к поверхностям
трения шарнира (рис.1)
производится
периодически через осевое и радиальное
отверстия в пальце 1.
Диаметр
отверстий назначают d1=
3…6
мм в зависимости от диаметра пальца d.
Отверстие
закрывается резьбовой пробкой
соответственно диаметром М5…8.
Распределение
смазки вдоль пальца (рис.1) осуществляют
различными способами:
а)
если направление реакции на палец
неопределенно, то во втулке штока 2
выполняют кольцевую канавку диаметром
D1
=
d+ 2
мм;
б)
если направление реакции на палец при
работе механизма изменяется в
пределах
=0…
180°, то на пальце выполняют продольную
канавку длиной
l=
l1-2 c,
где с
=5…10 мм, канавка должна отстоять от
предполагаемого места приложения
наибольшей по величине реакции на угол
φ1
=90°;
в)
если направление реакции на палец при
работе механизма изменяется в пределах
φ
= 0…360°
, то на пальце выполняют две продольные
канавки длиной
l=
l1-2 c,
где с
=
5…10 мм, канавки должны располагаться
диаметрально противоположно.
Соседние файлы в предмете [НЕСОРТИРОВАННОЕ]
- #
- #
- #
- #
- #
- #
- #
- #
- #
- #
- #
Источник
В большинстве разъемных соединений, применяемых в конструкции самолета, широко используются разного рода проушины. При проектировании надо учитывать, что любой стык является критическим местом и сделать его равнопрочным регулярному полотну без значительного увеличения массы очень сложно. К увеличению массы проушины ведет наличие концентрации напряжений в зоне отверстия, а масса проушин подвижных соединений увеличивается из-за снижения напряжения смятия под болтом и соответствующего увеличения размеров проушины.
Алгоритм проектировочного расчета проушины неподвижного соединения.
Расчетная схема проушины неподвижного соединения представлена на (рис. 2.1). Пусть задана сила Р, вызывающая разрыв проушины.
Рис. 2.1. Проушина
Расчет соединения типа «ухо-вилка» осуществляется по следующему алгоритму:
1. Определение площади сечения болта. Определяется площадь сечения болта из условия работы на срез:
где: — расчетная нагрузка на проушину;
вб — предел прочности материала болта на срез;
вб=(0,6…0,65)вб
— число плоскостей среза болта, .
2. Определение диаметра соединительного болта из условия среза. Диаметр болта определяется по следующей формуле:
где:-диаметр соединительного болта, уточняется по справочникам согласно отраслевых стандартов или нормалям.
3. Определение толщины проушины.
Толщина средней проушины уха или суммарная толщина двух крайних проушин вилки определяется из условия работы проушины на смятие, определяется ее толщина:
где см — допустимое напряжение смятия проушины может быть определено по формуле:
— коэфициент зависящий от типа соединения, =1…1,3
4. Определение остальных размеров проушины.
Осчтальные размеры проушины определяются из условия разрыва по сечению А- Необходимо учитывать, что из-за наличия отверстия в сечении А-А проушины, напряжения будут изменяться неравномерно. За разрушающее напряжение в этом случае принимается величина [],
где k — коэффициент, учитывающий концентрацию напряжений.
Приближенно k можно определить по эмпирической зависимости:
Более точное значение k можно определить по справочникам. Обычно, отношение параметров и выбирают в следующих пределах:
=c=1…1,4 и = 2…3
Тогда, площадь сечения проушины по сечении А-А из условия разрыва будет равна:
где вп — допустимое временное напряжение материала проушины.
Учитывая, что площадь сечения проушины можно определить:
; У=1,2Х;
Ширину перемычки (У) необходимо проверить из условия среза по плоскостям (У1-У2)
;
где ВП — предел прочности материала проушины на срез.
Необходимо соблюдение условия У<У;
Площадь сечения за проушиной определяют по выражению:
6. Программа расчета проушин неподвижного соединения.
Приведенный в разделе 2.1 алгоритм расчета проушины неподвижного соединения был реализован в виде программы PROUSH для вычислительной машины ПЭВМ на алгоритмическом языке ПАСКАЛ 7.0
В числовом материале программы используются характеристики алюминиевого сплава Д16 и стали 30ХГСА.
Решение задач по конструированию проушина с использованием программы PROUSH производится с помощью терминального комплекса автоматизированного программирования (ТЕКАП), разработанного на кафедре КиПЛА. ТЕКАП позволяет с помощью клавиатуры дисплея ПЭВМ задать исходные данные, отправить программу на решение и получить ответ на экране дисплея либо на бумаге в виде распечатки.
Для работы программы PROUSH необходимо ввести исходные данные (табл. 2.1).
Таблица 2.1
N п/п | Наименование величины | Еди- ница | Обозна- чение | Иденти- фикатор |
1 2 3 4 | Расчетная нагрузка на проушины Коэффициент, зависящий от типа соединения Отношение параметров Отношение параметров | Н — — — | P у/х в/d | Р MS C N |
В результате расчета получаются следующие параметры проушина (табл. 2.2).
Таблица 2.2
N п/п | Наименование величины | Еди- ница | Обозна- чение | Иденти- фикатор |
1 2 3 4 5 6 7 8 9 10 | Площадь сечения болта Диаметр болта Толщина проушины Площадь сечения проушины по сечении А-А Площадь сечения за проушины Ширина перемычки из условия разрыва проушины по плоскостям Потребная ширина проушины Ширина перемычки из условия среза проушины по плоскостям Коэффициент концентрации напряжений Ширина перемычки из условия среза проушины по плоскостям | мм2 мм мм мм2 мм2 мм мм мм — мм | Fб dб а Fn F1 x в У k У | SB DB A SP S1 X B Y KH Y1 |
Таблица 2.3. Таблица вариантов задания исходных данных
N:зад | 1 | 2 | 3 | 4 | 5 | 6 | 7 | 8 | 9 | 10 | 11 | 12 |
Р(кН) | 20 | 22 | 24 | 26 | 28 | 30 | 32 | 34 | 36 | 38 | 40 | 42 |
N:зад | 13 | 14 | 15 | 16 | 17 | 18 | 19 | 20 | 21 | 22 | 23 | 24 |
Р(кН) | 44 | 46 | 48 | 50 | 21 | 23 | 25 | 27 | 29 | 31 | 33 | 25 |
Источник
Инженерами АО «ЦИФРА» произведен расчет прочности пространственной траверсы по допускаемым напряжениям и по предельному состоянию, в ходе которого выявлены конструктивные недостатки и предложен новый вариант конструкции, отвечающий предъявляемым требованиям.
Целью расчета является проверка выполнения требований Заказчика: конструкция должна воспринимать рабочую нагрузку без возникновения пластических деформаций и иметь запас прочности по предельному состоянию не менее пятикратного.
Введение
Траверса — это съемное грузоподъемное оборудование, предназначенное для строповки длинномерных и крупногабаритных грузов. Траверсы предохраняют поднимаемые грузы от воздействия сжимающих усилий, которые возникают при использовании стропов.
По конструктивным особенностям различают линейные и пространственные траверсы. Линейные траверсы имеют вид линейной балки или сварной конструкции, выполненной из швеллера.
Пространственные траверсы изготавливаются в виде простейших ферм треугольной или прямоугольной формы. Пространственные траверсы позволяют поднимать грузы значительной массы и габаритов. Основной частью траверсы является балка или ферма, которая воспринимает изгибающие нагрузки. К балке подвешиваются канатные или цепные ветви.
Прочностные характеристики грузоподъемного оборудования должны соответствовать требованиям, установленным производителем. В нормах, устанавливающих требования к прочностным расчетам грузоподъемного оборудования, часто можно встретить требования к расчету как по допускаемым напряжениям, так и по предельному состоянию.
Расчет пространственной траверсы по предельному состоянию
Для выполнения расчётов прочности камеры насыщения использовался пакет программ Ansys 2020 R2. Подготовка геометрической модели произведена при помощи CAD-пакета Ansys SpaceClaim. Построение конечно-элементной сетки выполнено при помощи Ansys Meshing. Постановка задачи, выполнение расчёта и обработка результатов производились при помощи продукта Ansys Mechanical.
Конструкция пространственной траверсы представлена на рисунке ниже.
Про стропы
Строповка конструкции траверсы к крюку крана происходит за верхние проушины посредством цепей. Строповка грузка к конструкции траверсы производится за нижние проушины.
Цепи, за которые конструкция подвешивается за крюк крана, и стропы, за которые подвешивается поднимаемый груз, не являются предметом исследования, но для физичного моделирования прочности траверсы важно учесть их в расчетной модели.
Верхние цепи учтены в модели с помощью специальных элементов типа COMBIN14. Данный тип элемента позволяет устанавливать требуемую жесткость. Жесткость цепи может быть определена по формуле:
При моделировании строповки траверсы к крюку крана важно правильно учесть положение точки подвеса.
Для того чтобы получить достоверную информацию о напряженно-деформированном состоянии траверсы, необходимо правильно учесть в модели поднимаемый груз. Одним из преимуществ пространственных траверс является возможность производить захват груза за 3 и более точки. Применение траверсы во время подъема груза обеспечивает уменьшение или полное снятие изгибающих усилий, которые оказывают влияние на груз в случае подъема непосредственно с использованием стропов. Поднимаемый объект смоделирован в расчете условным грузом с центром тяжести, совпадающим с центром тяжести поднимаемого объекта, а нижние стропы в модели имеют вертикальное положение – это соответствует реальному положению строп.
В качестве нижних строп траверсы используются полиэстеровые слинги на 25 тонн. В данном исследовании они, как и верхние цепи, не являются объектом исследования, поэтому в модели они учтены с помощью специального типа конечного элемента LINK180, в котором учитывается работа слинга только на растяжение.
Граничные условия для траверсы с грузом представлены на рисунке ниже. Линии связей, моделирующие верхние цепи, закреплены в точке подвеса. Движение груза ограничено в направлениях оси X и Y, вращательные степени свободы заблокированы во всех направлениях.
Физико-механические свойства материалов
Элементы конструкции выполнены из низколегированной углеродистой стали повышенной прочности 09Г2С. В расчете по допускаемым напряжениям используется линейная модель материала. В расчете по предельному состоянию используется билинейная модель пластичности с изотропным упрочнением (показана на рисунке ниже), наклон первого участка прямой определяется исходя из упругих характеристик, которые описывают закон Гука, второй участок материала начинается со значения предела текучести, а угол наклона второго участка определяется касательным модулем пластичности. В рассмотренной задаче использованы значение модуля Юнга 200 ГПа, коэффициента Пуассона 0,3. Значение предела текучести для стали 09Г2С 295 МПа, предела прочности 405 МПа, касательного модуля 295 МПа.
Билинейная кривая деформирования материала
Более точно описать характер пластичности позволяет мультилинейная модель пластичности. Для задания мультилинейной модели пластичности требуемыми данными являются: модуль Юнга, коэффициент Пуассона и зависимость напряжения от относительной пластической деформации. В качестве входных данных используются результаты экспериментов по растяжению образцов: зависимость силы от удлинения испытуемого образца. Значение инженерных напряжений вычисляется путем деления удлинения на начальную длину образца. Но максимальная точка на получившейся кривой не описывает реального напряженного состояния в образце, поскольку не учтены геометрические эффекты, т.е. сужение образца. Адекватности модели можно достичь путем использования в ней диаграммы истинных напряжений. На рисунке ниже показано сравнение диаграмм инженерных и истинных напряжений. О том, как правильно задавать механические свойства материалов за пределом текучести подробно рассказывается в этой статье.
Расчет оборудования по допускаемым напряжениям
Расчет по допускаемым напряжениям предполагает упругое поведение материала, т.е. линейную зависимость между деформациями и напряжениями. Подобные расчеты имеют очень широкое применение в инженерной практике.
Методика расчета по допускаемым напряжениям основана на сравнении расчетных напряжений с допускаемыми. Величина допускаемых напряжений определяется путем деления значения предела текучести материала на коэффициент запаса.
В результате решения прочностного анализа в линейной постановке в модели могут наблюдаться точечные участки, в которых возникают очень высокие напряжения — они являются следствием сингулярности в модели. Обычно сингулярность возникает в местах приложения точечной нагрузки, на острых кромках или углах, а также из-за особенностей наложения связей, ограничивающих число степеней свободы. Сингулярность характеризуется высоким значением напряжения в одном элементе сетки, и при разбиении этой области на большее число элементов будут приводить лишь к росту напряжений, и в теории, напряжения в сингулярности будут стремиться к бесконечности.
Зачастую наличие таких областей в конструкции препятствует правильной оценке её НДС, поскольку напряжения, возникающие в месте сингулярности, не отражают реального напряженно-деформированного состояния конструкции. А в некоторых случаях величина напряжений, возникающих в месте сингулярности, может быть намеренно занижена расчетчиком путем изменения плотности сетки, что приведет к неверной оценке прочности конструкции.
На рисунке ниже приведены результаты расчета по допускаемым напряжениям грузоподъемного оборудования с различными плотностями сеток. Использование линейной модели в расчетах дает правильное представление о напряженно-деформированном состоянии конструкции в целом: величина и распределение этих напряжений не изменится при переходе к пластической модели материала, но в точках сингулярности определение величины напряжений является затруднительным. Сравнивая результаты расчета по допускаемым напряжениям, которые приведены ниже, можно заметить, как возрастают напряжения в точке сингулярности при измельчении сетки.
Расчет оборудования по предельному состоянию
В реальной конструкции невозможно возникновение бесконечных напряжений, поскольку при достижении значения предела текучести материал перейдет в стадию пластических деформаций, при которой зависимость напряжений от деформаций носит иной характер. При накоплении пластических деформаций в месте сингулярности будет происходить упрочнение. Это не будет опасным для конструкции, кроме случая образования пластического шарнира в сечении.
Расчет грузоподъемного оборудования по предельному состоянию подразумевает исследование поведения конструкции за пределом упругой зоны. Задачей расчета является определение величины нагрузки, при которой произойдет потеря несущей способности грузоподъёмного оборудования. Деформирование материала происходит в две стадии: на первой стадии происходит упругое деформирование, поведение материала подчиняется закону Гука. При достижении напряжений в конструкции предела текучести в конструкции начинают развиваться пластические деформации при постоянном напряжении. Область пластических деформаций постепенно увеличивается, пока не захватывает целиком поперечное сечение конструкции – образуется пластический шарнир, либо его более сложная пространственная реализация, сопровождающаяся неограниченным ростом перемещений конструкции без увеличения нагрузки.
Решение нелинейной задачи в ПО ANSYS
В основе решения нелинейных задач в ANSYS реализован итеративный алгоритм Ньютона-Рафсона. Каждая итерация называется равновесной. Фактическая зависимость между нагрузкой и перемещением заранее не известна. В процессе решения нелинейной задачи методом Ньютона-Рафсона выполняется ряд линейных аппроксимаций с корректировками. В настройках решателя можно включить отображение невязок, и увидеть, в каких местах модели возникает дисбаланс внешних и внутренних сил. Пример отображения невязок Ньютона-Рафсона показан на рисунке ниже.
При нагружении конструкции силой на первом подшаге к конструкции прикладывается полная сила (или ее часть, в зависимости от настройки решателя). Из полученных значений перемещений вычисляются внутренние силы, возникающие в конструкции, а на основании текущих условий вычисляется новая матрица жесткости. Если внешняя приложенная нагрузка не равна внутренним силам, возникающим в конструкции, система считается не равновесной. Разница этих сил называется остаточными силами или невязкой. Для того, чтобы решение сошлось, остаточные силы должны быть достаточно малы. Эти итерации продолжаются до тех пор, пока система не достигнет равновесия и решение будет считаться сошедшимся. Такое нагружение называется «мягким».
При действии на конструкцию постепенно увеличивающимся перемещением, внутренние силы вычисляются исходя из величины приложенного перемещения. Этот вариант нагружения является более стабильным и носит название «жесткое нагружение».
При использовании мягкого нагружения и потере несущей способности конструкции происходит неограниченных рост перемещений, тогда как при жестком нагружении граничные условия удерживают конструкцию на месте. Именно в этом и проявляется стабильность жесткого нагружения.
Поэтому в данном случае нагружение траверсы производится посредством жесткого нагружения вплоть до потери несущей способности конструкции. Информация о силах реакций, возникающих в проушинах траверсы, даст представление о нагрузке, при которой происходит потеря несущей способности грузоподъемного оборудования.
Определение несущей способности траверсы
По результатам расчета определено, что в конструкции произойдет потеря несущей способности при нагрузке, превышающей максимальную рабочую нагрузку в 4,8 раза.
На рисунке ниже показано распределение полей пластических деформаций при нагружении пространственной траверсы нагрузкой, в 4,8 раза превышающую максимальную рабочую нагрузку. Это недостаточный коэффициент запаса, поскольку требования к конструкции предполагают не менее пятикратный запас прочности для деталей траверсы.
Ниже приведены ракурсы, на которых показаны места, в которых происходит излом конструкции. Развитие пластических деформаций и излом конструкции происходит в местах, где ребра жесткости своими острыми концами упираются в балку. Подобное конструктивное решение можно классифицировать как конструкторскую ошибку, поскольку такая конфигурация ребер приводит к образованию концентраторов напряжений, в которых при достижении предела текучести пластические деформации распространяются по всему сечению конструкции, что приводит к образованию пластического шарнира и снижает несущую способность конструкции.
Для того чтобы снизить величину пластических деформаций и увеличить запас прочности конструкции, инженерами АО «ЦИФРА» предложен вариант локальных изменений в конструкции. Ребро продлено до проушин, а сами проушины удлинены во избежание ограничения доступности отверстия при строповке. Внесение этих изменений в конструкцию увеличивает массу грузоподъемного оборудования на 0,5%.
Поверочный расчет измененной конструкции пространственной траверсы по предельному состоянию показал, что в конструкции произойдет образование пластического шарнира и потеря несущей способности при нагрузке, превышающей максимальную рабочую нагрузку в 6,8 раз.
На рисунке ниже показано распределение полей пластических деформаций при нагружении траверсы нагрузкой, в 6,8 раз превышающую максимальную рабочую нагрузку.
Ниже приведен график зависимости действующей нагрузки от вертикального перемещения в проушине для исходного варианта конструкции и для варианта конструкции с внесенными изменениями. Удлинение ребер жесткости до проушин позволило увеличить запас прочности грузоподъемного оборудования на 40%.
Заключение
Проведен расчет грузоподъемного оборудования по допускаемым напряжениям и по предельному состоянию. Найденный запас прочности траверсы по несущей способности при действии максимально возможной нагрузки оказался недостаточным для выполнения условий прочности. Установлено, что причиной занижения несущей способности конструкции является конструкторская ошибка, вследствие чего предложен вариант локального изменения геометрии конструкции. Предложенные конструктивные изменения увеличили массу конструкции на 0,5%, что позволило увеличить запас прочности грузоподъемного оборудования по несущей способности на 40% и обеспечить выполнение условия прочности.
Источник