Прочность на разрыв растяжение
14Ноя
By: Семантика
Без рубрики
Comment: 0
Содержание статьи
- Предел прочности
- Как производится испытание на прочность
- Виды ПП
- Предел прочности на растяжение стали
- Предел текучести и временное сопротивление
- Усталость стали
- Предел пропорциональности
- Как определяют свойства металлов
- Механические свойства
- Классы прочности и их обозначения
- Формула удельной прочности
- Использование свойств металлов
- Пути увеличения прочностных характеристик
При строительстве объектов обязательно необходимо использовать расчеты, включающие подробные характеристики стройматериалов. В обратном случае на опору может быть возложена слишком большая, непосильная нагрузка, из-за чего произойдет разрушения. Сегодня поговорим о пределе прочности материала при разрыве и натяжении, расскажем, что это такое и как работать с этим показанием.
Предел прочности
ПП – будем использовать это сокращение, а также можно говорить об официальном сочетании «временное сопротивление» – это максимальная механическая сила, которая может быть применена к объекту до начала его разрушения. В данном случае мы не говорим о химическом воздействии, но подразумеваем, что нагревание, неблагоприятные климатические условия, определенная среда могут либо улучшать свойства металла (а также дерева, пластмассы), либо ухудшать.
Ни один инженер не использует при проектировании крайние значения, потому что необходимо оставить допустимую погрешность – на окружающие факторы, на длительность эксплуатации. Рассказали, что называется пределом прочности, теперь перейдем к особенностям определения.
Как производится испытание на прочность
Изначально особенных мероприятий не было. Люди брали предмет, использовали его, а как только он ломался, анализировали поломку и снижали нагрузку на аналогичное изделие. Теперь процедура гораздо сложнее, однако, до настоящего времени самый объективный способ узнать ПП – эмпирический путь, то есть опыты и эксперименты.
Все испытания проходят в специальных условиях с большим количеством точной техники, которая фиксирует состояние, характеристики подопытного материала. Обычно он закреплен и испытывает различные воздействия – растяжение, сжатие. Их оказывают инструменты с высокой точностью – отмечается каждая тысячная ньютона из прикладываемой силы. Одновременно с этим фиксируется каждая деформация, когда она происходит. Еще один метод не лабораторный, а вычислительный. Но обычно математический анализ используется вместе с испытаниями.
Определение термина
Образец растягивается на испытательной машине. При этом сначала он удлиняется в размере, а поперечное сечение становится уже, а затем образуется шейка – место, где самый тонкий диаметр, именно здесь заготовка разорвется. Это актуально для вязких сплавов, в то время как хрупкие, к ним относится чугун и твердая сталь, растягиваются совсем незначительно без образования шейки. Подробнее посмотрим на видео:
Виды ПП
Временное сопротивление разрыву определяют по различным воздействиям, согласно этому его классифицируют по:
- сжатию – на образец действуют механические силы давления;
- изгибу – деталь сгибают в различные стороны;
- кручению – проверяется пригодность для использования в качестве крутящегося вала;
- растяжению – подробный пример проверки мы привели выше.
Предел прочности на растяжение стали
Стальные конструкции давно заменили прочие материалы, так как они обладают отличными эксплуатационными характеристиками – долговечностью, надежностью и безопасностью. В зависимости от применяемой технологии, он подразделяется на марки. От самой обычной с ПП в 300 Мпа, до наиболее твердой с высоким содержанием углерода – 900 Мпа. Это зависит от двух показателей:
- Какие способы термообработки применялись – отжиг, закалка, криообработка.
- Какие примеси содержатся в составе. Одни считаются вредными, от них избавляются для чистоты сплава, а вторые добавляют для укрепления.
Предел текучести и временное сопротивление
Новый термин обозначается в технической литературе буквой Т. Показатель актуален исключительно для пластичных материалов и обозначает, как долго может деформироваться образец без увеличения на него внешней нагрузки.
Обычно после преодоления этого порога кристаллическая решетка сильно меняется, перестраивается. Результатом выступают пластические деформации. Они не являются нежелательными, напротив, происходит самоупрочнение металла.
Усталость стали
Второе название – предел выносливости. Его обозначают буквой R. Это аналогичный показатель, то есть он определяет, какая сила может воздействовать на элемент, но не в единичном случае, а в цикле. То есть на подопытный эталон циклично, раз за разом действуют определенные давления. Среднее количество повторений – 10 в седьмой степени. Именно столько раз металл должен без деформаций и потери своих характеристик выдержать воздействие.
Если проводить эмпирические испытания, то потребуется множество времени – нужно проверить все значения силы, прикладывая ее по множеству циклов. Поэтому обычно коэффициент рассчитывается математически.
Предел пропорциональности
Это показатель, определяющий длительность оказываемых нагрузок к деформации тела. При этом оба значения должны изменяться в разный степени по закону Гука. Простыми словами: чем больше оказывается сжатие (растяжение), тем сильнее деформируется образец.
Значение каждого материала находится между абсолютной и классической упругостью. То есть если изменения обратимы, после того как сила перестала действовать (форма стала прежняя – пример, сжатие пружины), то такие параметры нельзя называть пропорциональными.
Как определяют свойства металлов
Проверяют не только то, что называют пределом прочности, но и остальные характеристики стали, например, твердость. Испытания проводят следующим образом: в образец вдавливают шарик или конус из алмаза – наиболее прочной породы. Чем крепче материал, тем меньше след остается. Более глубокие, с широким диаметром отпечатки остаются на мягких сплавах. Еще один опыт – на удар. Воздействие оказывается только после заранее сделанного надреза на заготовке. То есть разрушение проверяется для наиболее уязвимого участка.
Механические свойства
Различают 5 характеристик:
- Предел прочности стали при растяжении и на разрыв это – временное сопротивление внешним силам, напряжение, возникающее внутри.
- Пластичность – это возможность деформироваться, менять форму, но сохранять внутреннюю структуру.
- Твердость – готовность встретиться с более твердым материалом и не получить значительных ущербов.
- Ударная вязкость – способность сопротивляться ударам.
- Усталость – длительность сохранения качеств под воздействием цикличных нагрузок.
Классы прочности и их обозначения
Все категории записаны в нормативных документах – ГОСТах, по ним все российские предприниматели изготавливают любой металлопрокат и прочие металлические изделия. Вот соответствие обозначения и параметра в таблице:
Класс | Временное сопротивление, Н/мм2 |
265 | 430 |
295 | 430 |
315 | 450 |
325 | 450 |
345 | 490 |
355 | 490 |
375 | 510 |
390 | 510 |
440 | 590 |
Видим, что для некоторых классов остается одинаковыми показатели ПП, это объясняется тем, что при равных значениях у них может различаться текучесть или относительное удлинение. В зависимости от этого возможна различная максимальная толщина металлопроката.
Формула удельной прочности
R с индексом «у» – обозначение данного параметра в физике. Рассчитывается как ПП (в записи – R) поделенное на плотность – d. То есть этот расчет имеет практическую ценность и учитывает теоретические знания о свойствах стали для применения в жизни. Инженеры могут сказать, как меняется временное сопротивление в зависимости от массы, объема изделия. Логично, что чем тоньше лист, тем легче его деформировать.
Формула выглядит так:
Ry = R/d
Здесь будет логичным объяснить, в чем измеряется удельный предел прочности. В Н/мм2 – это вытекает из предложенного алгоритма вычисления.
Использование свойств металлов
Два важных показателя – пластичность и ПП – взаимосвязаны. Материалы с большим первым параметром намного медленнее разрушаются. Они хорошо меняют свою форму, подвергаются различным видам металлообработке, в том числе объемной штамповке – поэтому из листов делают элементы кузова автомобиля. При малой пластичности сплавы называют хрупкими. Они могут быть очень твердыми, но при этом плохо тянуться, изгибаться и деформироваться, например, титан.
Сопротивление
Есть два типа:
- Нормативное – прописано для каждого типа стали в ГОСТах.
- Расчетное – получается после вычислений в конкретном проекте.
Первый вариант скорее теоретический, для практических задач используется второй.
Пути увеличения прочностных характеристик
Есть несколько способов это сделать, два основных:
- добавка примесей;
- термообработка, например, закал.
Иногда они используются вместе.
Общие сведения о сталях
Все они обладают химическими свойствами и механическими. Ниже подробнее поговорим о способах увеличения прочности, но для начала представим схему, на которой представлены все разновидности:
Также посмотрим более подробное видео:
Все они обладают химическими свойствами и механическими. Ниже подробнее поговорим о способах увеличения прочности, но для начала представим схему, на которой представлены все разновидности:
Углерод
Чем больше углеродность вещества, тем выше твердость и меньше пластичность. Но в составе не должно быть более 1% химического компонента, так как большее количество приводит к обратному эффекту.
Марганец
Очень полезная добавка, но при массовой доле не более двух процентов. Обычно Mn добавляют для улучшения качеств обрабатываемости. Материал становится более подвержен ковке и свариванию. Это объясняется вытеснением кислорода и серы.
Кремний
Эффективно повышает прочностные характеристики, при этом не затрагивая пластичность. Максимальное содержание – 0,6%, иногда достаточно и 0,1%. Хорошо сочетается с другими примесями, в совокупности можно увеличить устойчивость к коррозии.
Азот и кислород
Если они попадают в сплав, но ухудшают его характеристики, при изготовлении от них пытаются избавиться.
Легирующие добавки
Также можно встретить следующие примеси:
- Хром – увеличивает твёрдость.
- Молибден – защищает от ржавчины.
- Ванадий – для упругости.
- Никель – хорошо влияет на прокаливаемость, но может привести к хрупкости.
Эти и другие химические вещества должны применяться в строгих пропорциях в соответствии с формулами. В статье мы рассказали про предел прочности (кратковременное сопротивление) – что это, и как с ним работать. Также дали несколько таблиц, которым можно пользоваться при работе. В качестве завершения, давайте посмотрим видеоролик:
Чтобы уточнить интересующую вас информацию, свяжитесь с нашими менеджерами по телефонам 8 (908) 135-59-82; (473) 239-65-79; 8 (800) 707-53-38. Они ответят на все ваши вопросы.
Источник
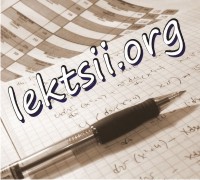
Когда материал растягивают в разные стороны, возникает стресс растяжения, и в результате материал разрывается. Предельное значение силы, при которой происходит разрыв, называется пределом прочности на растяжение (прочность на разрыв).
Предел прочности на растяжение измеряют у таких материалов, как сплавы, композиты, керамические материалы и пластики. Он измеряется в МПа, это сила, приложенная к площади, т.е. кг/см2. Чем выше это значение, тем материал более устойчив к усилиям на растяжение.
Во время испытания перед разрушением материал проходит «стадию колокола» (см. рис. 2).
Это испытание помогает понять прочность материала.
Рис. 1 Рис. 2 Рис. 3 |
Прочность на сжатие (МПа)
Сдавливая образец материала, имитируется жевательная нагрузка на конструкцию. Во время испытания материал сдавливается, приобретает форму бочки (Рис.5). В результате нагрузки возникает стресс растяжения в горизонтальных направлениях и в итоге материал разрушается.
Прочность на сжатие измеряется в МПа. Чем выше значение, тем лучше сопротивление материала нагрузкам на сжатие и тем материал более стабильный.
Проводят измерения для композитных материалов и цементов.
Рис. 4 Рис. 5 Рис. 6 |
3. Модуль эластичности (ГПа) / Модуль Е / Модуль Юнга / Модуль гибкости.
Свойства твердости и упругости материалов измеряются в ГПа.
Модуль эластичности отражает сопротивление материала внешней нагрузке, в данном случае на изгиб. С материалом не происходит необратимой деформации, после устранения внешней нагрузки он возвращается в исходное состояние. То есть в данном случае, в отличие от других испытаний, материал не разрушается.
Трех-точечный тест на изгиб. Брусок материала устанавливается на 2 опоры и прикладывают к нему силу F (рис. 7 и 8).
Нагрузка увеличивается только до того момента, когда материал начинает изгибаться (см. рис. 9). Чем выше это значение, тем материал более жесткий.
Рис. 8 | Рис. 9 |
Жесткость важна при выборе реставрационного материала, поскольку совсем не нужно, чтобы материал существенно отклонялся под воздействием нагрузки. Типичный пример, это внутрипульпарные штифты. Его жесткость должна соответствовать жесткости дентина.
Для эластичных оттискных материалов желательны, напротив, малые значения, поскольку в этом случае оттиск будет легко извлекаться изо рта пациента.
Прочность на изгиб (МПа)
Для ее измерения также используется трех-точечный тест. В данном случае нагрузка прикладывается, пока материал не разрушится (см. Рис. 11).
Прочность на изгиб – это способность материала быть устойчивым к переломам при нагрузке. Она измеряется в МПа, мегапаскалях.
Рис. 10 | Рис. 11 |
Данное испытание напоминает нагрузку на мост. Высокое значение прочности на изгиб означает, что мост обладает высокой устойчивостью к перелому.
5. Предел усталости – циклические нагрузки
Сначала проводится испытание на прочность на изгиб для определения предельной прочности материала (МПа). Затем берется нагрузка ниже, чем вышеуказанный предел прочности. В той же конфигурации трех-точечной нагрузки последовательно циклически нагружается материал. Затем отмечают, сколько циклов выдерживает материал до поломки.
Данный тест имитирует жевательные нагрузки на мост. Чем больше циклов выдерживает материал, тем лучше.
Усталость материалов. При воздействии большого числа циклических нагрузок на протез может наступить разрушение материала. Разрушающее напряжение (предел усталости) оказывается при этом значительно ниже предела прочности.
Причины усталости до сих пор не вполне ясны. Микроскопическое исследование образцов, подвергнутых многократной переменной нагрузке, показало, что в зернах материала после некоторого числа нагружений появляется ряд черточек, свидетельствующих о наличии сдвигов частей зерен. Под дальнейшим действием нагрузки черточки превращаются в тончайшие трещинки, которые сливаются в трещину. Около нее и сосредоточивается дальнейшее разрушение.
Трещина с каждым нагружением растет, и, когда поперечное сечение достаточно уменьшится, наступает разрушение. Образовавшаяся трещина действует подобно выточке, т. е. вызывает концентрацию напряжения и снижает сопротивление. Момент разрушения приближается незаметно. Конструкция, которой грозит разрушение, работает безупречно, но наконец внезапно происходит разрушение, причем при незначительной нагрузке.
Очень часто причинами усталостных изломов служат резкие изменения формы деталей (резкие переходы по толщине, надрезы, трещины на поверхности, поры и т. д.), вызывающие концентрацию напряжения. Так как усталостные трещины появляются вокруг этих участков, то борьба с усталостью, помимо подбора более прочных материалов, заключается в упрочнении его поверхности. Так, для металлов это достигается химико-термической обработкой, механической обработкой (шлифовка, полировка), закалкой токами высокой частоты. Эти меры позволяют повысить предел усталости на несколько десятков процентов. В отношении пластмасс большое значение имеет также правильный режим полимеризации, не вызывающий образования пор в протезах.
Предел прочности некоторых стоматологических материалов:
Материал | Прочность на растяжение (МРа) | Прочность на сжатие (МРа) |
Дентин зуба | ||
Эмаль зуба | ||
Стом.амальгама | 48-69 | 310-483 |
Золото | 414-828 | — |
Композиты | 34-62 | 200-345 |
Ненаполненные акриловые пластмассы | ||
Фарфор | ||
Хромо-никелевый сплав | — |
Упругость. Способность материала изменять форму под действием внешней нагрузки и восстанавливать форму после снятия этой нагрузки называется упругостью. Характерным примером упругих свойств материала может служить изгиб стальной проволоки, растяжение металлической пружины, сдавления протеза из полиамидной пластмассы, куска гидроколоидной массы. После удаления силы все эти тела приобретают свою форму. Но возврат к прежней форме может произойти лишь в случае, если приложенная сила не превысила определенной величины, называемой пределом упругости. Пределом упругости называют максимальную нагрузку, при которой материал после деформации и снятия нагрузки полностью восстанавливает свою форму и размеры. Если нагрузка превысит предел упругости, то после снятия ее материал полностью не восстановится до первоначального состояния, появится остаточная деформация.
Материалы, применяемые для изготовления зубных протезов и аппаратов, обладают различной упругостью. Некоторые конструкции должны обязательно обладать упругими свойствами, так как они постоянно находятся под силовым воздействием, а появление остаточной деформации делает их непригодными (кламмеры, дуги, базисы протезов и т. д.).
В других случаях проявление упругих свойств мешает проведению некоторых технологических этапов. Так, например, штамповка коронок, возможна, если металл будет находиться в состоянии наименьшей упругости.
Металлы могут по-разному проявлять упругость в зависимости от их механической и термической обработки. Сталь увеличивает упругость при обработке ее молотком или при протягивании, а также при закаливании.
Все материалы обладают упругими свойствами в определенных температурных интервалах. Для металлов эти интервалы достигают сотен градусов, у пластмасс они значительно меньше. Для базисных пластмасс они измеряются десятками градусов.
Упругость материала определяют на образцах, которые укрепляют в приборах типа гидравлического
пресса и подвергают нагружению. Измеряют изменение длины образца при максимальной нагрузке, не вызывающей остаточной деформации, после снятия которой образец принимает первоначальную длину. Расчет ведется на 1 мм2.
Понятно, что при определении нагрузок, допускаемых на различные участки протезов, знание предела упругости материала, из которого он изготовлен, является совершенно необходимым, так как нагрузка выше предела упругости приводит к изменению формы протеза, а следовательно, и к невозможности пользования им.
Если продолжать нагружать образец, то он постепенно начинает удлиняться, а его поперечное сечение становится меньше, причем по снятии нагрузки образец не возвращается к прежним размерам. Чем больше образец способен удлиняться, а его поперечное сечение сужаться, тем пластичнее материал.
В противоположность пластичным материалам хрупкие материалы под действием нагрузки разрушаются без изменения формы. Хрупкость, как правило, — свойство отрицательное, поэтому в ортопедической стоматологии чаще всего употребляют не только прочные и упругие материалы, но и в определенной мере пластичные.
Пластичность. Способность материала, не разрушаясь, изменять форму под действием нагрузок и сохранять эту форму после того, как нагрузка перестает действовать. Этим свойством обладают многие оттискные массы, воск, гипс, металлы.
Все пластичные материалы, таким образом, имеют резко выраженную остаточную деформацию. Пластичность необходима оттискным материалам, металлам, используемым для получения изделий методом штамповки, пластмассам, из которых формируются базисы протезов, пломбировочным материалам.
Иногда материал выбирают лишь благодаря его свойству приобретать пластичное состояние. Это относится в первую очередь к оттискным материалам, пластмассам. Для получения максимальной пластичности металла его подвергают особой термической обработке — отжигу, воск и оттискные массы подогревают, гипс смешивают с водой и т. д. Обычно обработка, повышающая пластичность, снижает сопротивление деформированию и наоборот.
Вязкость. Способность материала под действием растягивающих нагрузок вытягиваться. Этот вид деформации характеризуется тем, что исследуемый образец увеличивается по размерам в направлении приложенной силы (обычно по длине) и суживается в поперечном сечении.
Некоторые материалы обладают большой вязкостью (золото, серебро, железо и др.). Другие этой способностью не обладают (чугун, фарфор и др.). Они относятся к группе хрупких материалов.
Таким образом, хрупкость является свойством, противоположным вязкости.
При испытании различных материалов, в частности пластмасс, широко используют методику определения ударной вязкости. Удельной ударной вязкостью называется работа, затраченная на разрушение образца, деленная на площадь его поперечного сечения. Определение ударной вязкости производится на маятниковом копре MK-0,5-1. Прибор состоит из массивного основания, на котором смонтировано устройство маятникового типа. Маятник со сменным грузом (10—15—30 кг), укрепленный на оси станины, закрепляют на определенной высоте с помощью защепки. По освобождении зажима маятник свободно падает и производит удар по образцу. Чем прочнее образец, тем на меньшую высоту поднимается маятник после удара, т. е. тем большая работа была затрачена на ударное разрушение образца. Чем меньше ударная вязкость, тем более хрупким является материал.
Приведенные механические свойства материалов позволяют определить жесткость материалов. Способность элементов конструкции сопротивляться деформациям под действием внешних сил называется жесткостью.
Следует помнить, что при расчетах необходимых размеров деталей конструкции при предполагаемой нагрузке всегда придерживаются правила, что материал не должен не только разрушаться, но и деформироваться. Поэтому при расчетах всегда исходят из четырехкратного запаса прочности, т. е. если предел прочности углеродистой стали равен 90 кг/мм2, то допустимая нагрузка должна быть 22—23 кг/мм2. Если же рабочая нагрузка превышает эти цифры, то следует увеличивать размеры данной детали. Так, например, если нам известно, что сила, приложенная к протезу в момент разжевывания, равна 60 кг, а предел прочности пластмассы составляет 1000 кг/см2, то пластинка должна иметь в самой наименьшей части ширину, равную 2,5 см, при толщине 1 мм.
Литература:
1. Попков В.А. Стоматологическое материаловедение: Учебное пособие/ В.А. Попков. О.В.Нестерова, В.Ю.Решетняк, И.Н.Аверцева.//М. – МЕДпресс-информ. – 2009. – 400с.
2. Крег Р. Стоматологические материалы: свойства и применение/ Р.Крег, Дж.Пауэрс, Дж.Ватага// — 2005. – 304с.
3. https://article-factory.ru/medicina/zubotehnicheskoe-materialovedenie/139-mehanicheskie-svojstva.html
4. www.infodent.ru
Дата добавления: 2015-10-27; просмотров: 12471 | Нарушение авторских прав | Изречения для студентов
Читайте также:
Рекомендуемый контект:
Поиск на сайте:
© 2015-2021 lektsii.org — Контакты — Последнее добавление
Источник