Нагрузка на сварной шов растяжение
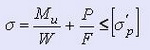
В конструкциях из металла зачастую необходимо соединить между собой отдельные детали, для того чтобы это осуществить прибегают к использованию сварных швов. Это один из самых простых и недорогих способов, отличающийся высоким качеством. Параметры у каждого сварного соединения разные, все зависит от используемого металла, его толщины и т.д. Поэтому в каждом отдельном случае необходимо произвести индивидуальный расчет на прочность сварных соединений. Эти вычисления помогут выявить характеристики сварного шва на данный момент.
Общие сведения
Как уже отмечалось, сварные швы являются одними из самых прочных среди существующих неразъемных соединений. Они возникают в результате воздействия сил молекулярного сцепления, которое является результатом сильного нагрева до расплавления деталей в месте их сцепления или нагрева деталей до пластического состояния, посредством механического усилия.
Несмотря на прочность и надежность сварного шва, у подобного соединения выделяется и ряд недочетов: из-за того, что нагревается и охлаждается соединение неравномерно, может наблюдаться остаточное напряжение. Помимо этого, в процессе сварки могут образовываться некоторые дефекты, например, трещины или непровары. Все это негативно сказывается на прочности сварных соединений.
Первоначальный расчет сварных швов на прочность производят на этапе составления проекта. Этому моменту стоит уделить особое внимание, поскольку важно выбрать материалы, которые будут надежными и прочными и смогут выдержать определенные нагрузки.
Если произвести верный расчет на прочность получившегося шва, то можно определить необходимое количество расходуемого материала.
Расчет сварных швов на прочность
Для того, чтобы произвести расчет сварных соединений и вычислить коэффициент прочности сварного шва, надо произвести точный замер всех показателей (форма, размер, положение в пространстве).
Осуществить сварку можно разными способами. На сегодняшний день наибольшей популярностью пользуются следующие виды сварки:
- электрическая, которая в свою очередь подразделяется на дуговую и контактную,
- газовая.
Также выделяются: ручная, полуавтоматическая, автоматическая сварка.
Учитывая тот фактор, каким образом размещаются элементы, которые подвергаются сварке, выделяются такие типы соединений: стыковые, угловые, нахлесточные, тавровые.
Для каждого из вышеизложенных типов расчет на прочность проводится индивидуально.
Стыковые швы
Если необходимо высчитать коэффициент прочности сварного шва, в первую очередь, нужно обратить внимание на такой параметр как номинальное сечение, при этом учитывать утолщения швов, образуемых во время сварки не нужно. Вычисление производится исходя из данных о сопротивлении материалов, которые образуются в сплошных балках.
Когда касательные, нормальные напряжения начнут оказывать непосредственное влияние на соединения, то для расчета эквивалентного напряжения следует воспользоваться формулой:
Условие прочности можно представить следующим образом: σЭ ≤ [σ’]P
Для поиска данных этого параметра ниже представлена таблица.
Метод сварки | Допускаемые напряжения | ||
При растяжении [σ’]р | При сжатии [σ’]еж | При сдвиге [τ’]ср | |
Автоматическая, ручная электродами Э42А и Э50А | [σ]р | [σ]р | 0,65 [σ]р |
Ручная электродами обычного качества | 0,9 [σ]р | [σ]р | 0,6 [σ]р |
Контактная точечная | 0,5 [σ]р |
Угловые швы
Соединение угловых сварных швов чаще всего осуществляется с поперечным сечением. Оба края соотносятся друг к другу 1:1. Поскольку сторона сечения называется катет сварного шва, на всех схемах и формулах она имеет обозначение «К». Зачастую шов деформируется и разрушается в самом маленьком месте сечения (опасное сечение), оно наиболее слабое, и проходит через биссектрису прямого угла. В таком сечении габариты (размер) шва определяются как β*К. Еще один важный показатель – длина шва (а). С помощью этих показателей можно узнать какую нагрузку способен выдержать сварной шов.
Рассмотрим примеры.
Если процесс сварки осуществлялся в автоматическом, полуавтоматическом или ручном режиме, то β будет равняться 0,7. Таким образом, получится шов в форме равнобедренного треугольника. В случае, когда процесс сварки происходил в полуавтоматическом режиме, но подход был не один, а несколько (2 или 3), то β уже будет равен 0,8; для такого же случая, но при автоматическом режиме β=0,9, а для автоматической однопроходной сварки — β=1,1. Требуется принимать К <δmin. В машиностроении общего назначения К, как правило, ≥ 3 мм.
Обратите внимание! Расчет на прочность сварных соединений углового типа должен производиться исключительно по касательным напряжениям.
Для этого необходимо узнать общее касательное напряжение. Чтобы узнать этот показатель надо определить самую нагруженную точку в данном сечении. После чего, показатели всех напряжений, находящихся в нем суммируются.
Для того, что найти коэффициент прочности сварного шва и узнать какую нагрузку он способен выдержать, надо иметь исходные данные. Однако, только этих сведений недостаточно. Важно рассчитать все верно и последовательно.
- На первом этапе нужно узнать все показатели, отличающие данное сварное соединение: форма, размер, положение в пространстве.
- После, опасное сечение — это сечение с наибольшим напряжением, нужно повернуть на плоскость, которая непосредственно контактирует со свариваемой деталью. После того, как вы его повернете, образуется новое расчетное сечение.
- На следующем этапе нужно определиться с местом положения центра масс на сечении, образовавшемся в результате поворота (расчетном сечении).
- Внешнюю приложенную нагрузку надо переместить в центр масс.
- Следующее, что необходимо сделать – это узнать показатели напряжения, образующегося в расчетном сечении под воздействием поперечной и нормальной силы, а также крутящего и изгибающего момента.
- Далее нужно найти самую нагруженную точку в сечении. Именно здесь надо суммировать все полученные нагрузки, оказывающие влияние на поверхность и в итоге вы узнаете общую итоговую нагрузку, которой будет подвергаться шов.
- Затем нужно произвести расчет допускаемого напряжения, которое будет воздействовать на шов.
- И заключительный этап состоит в сравнении допустимого напряжения и суммарного. Таким образом, вы получите размеры, которые максимально подходят для выбранной вами конструкции.
Подводя итог важно отметить, что производить расчет сварного шва на прочность обязательно нужно. Ведь верно высчитанные параметры обеспечат вам надежные соединения.
[Всего: 2 Средний: 3/5]
Источник
СТЫКОВОЕ СОЕДИНЕНИЕ С ПРЯМЫМ ШВОМ
(рис. 1, а).
Допускаемая сила для соединения при растяжении
Р1 = [σ’p]·L·S ,
то же при сжатии
Р2 = [σ’сж]·L·S ,
где,
[σ’p] и [σ’сж] — допускаемые напряжения для сварного шва соответственно при растяжении и сжатии.
При расчете прочности все виды подготовки кромок в стыковых соединениях принимают равноценными.
СТЫКОВОЕ СОЕДИНЕНИЕ С КОСЫМ ШВОМ
(рис. 1, б).
Допускаемая сила для соединения при растяжении
То же при сжатии
При β = 45° — соединение равнопрочно целому сечению.
НАХЛЕСТОЧНОЕ СОЕДИНЕНИЕ
(рис. 2).
Соединения выполняют угловым швом. В зависимости от напряжения шва относительно направления шва относительно направления действующих сил угловые швы называют лобовыми (см. рис. 2, а), фланговыми (см. рис. 2. б), косыми (см. рис. 2. в) и комбинированными (см. рис. 2, г).
Максимальную длину лобового и косого швов не ограничивают. Длину фланговых швов следует принимать не более 60К, где К — длина катета шва. Минимальная длина углового шва 30 мм; при меньшей длине дефекты в начале и в конце шва значительно снижают его прочность.
Минимальный катет углового шва Кmin принимают равным 3 мм, если толщина металла S >= 3 мм.
Допускаемая сила для соединения
где, [τср] — допускаемое напряжение для сварного шва на срез;
К — катет шва;
L — весь периметр угловых швов;
— для лобовых швов L = l; для фланговых L = 2l1;
— для косых L = l/sinβ;
— для комбинированных L = 2l1 + l.
СОЕДИНЕНИЕ НЕСИММЕТРИЧНЫХ ЭЛЕМЕНТОВ
(рис. 3).
Силы, передаваемые на швы 1 и 2, находят из уравнений статики
Необходимая длина швов
где,
[τ’ср] — допускаемое напряжение для сварного шва на срез;
К — катет шва.
Примечание: Допускается увеличение l2 до размера l1.
ТАВРОВОЕ СОЕДИНЕНИЕ
Наиболее простое в технологическом отношении.
Допускаемая сила для растяжения
Р = 0,7 [τ’ср] KL,
где,
[τ’ср] — допускаемое напряжение для сварного шва на срез;
К — катет шва, который не должен превышать 1,2S (S — наименьшая толщина свариваемых элементов).
Наиболее обеспечивающее лучшую передачу сил.
Допускаемая сила для растяжения
Р1 = [σ’p]·L·S ,
то же при сжатии
Р2 = [σ’сж]·L·S ,
где,
[σ’p] и [σ’сж] — допускаемые напряжения для сварного шва соответственно при растяжении и сжатии.
СОЕДИНЕНИЕ С НАКЛАДКАМИ
Сечение накладок, обеспечивающее равнопрочность целого сечения (см. рис. 6)
где,
F — сечение основного металла; [σp] — допускаемое напряжение при растяжении основного металла; [σ’p] — допускаемое напряжение для сварного шва при растяжении.
Сечение накладки, обеспечивающее равнопрочность целого сечения (см. рис. 7):
где,
[τ’cp] — допускаемое напряжение для сварного шва на срез.
СОЕДИНЕНИЕ С ПРОРЕЗЯМИ
Применяют лишь в случаях, когда угловые швы недостаточны для скрепления.
Рекомендуется a = 2S , l = (10 ÷ 25)S.
Допускаемая сила, действующая на прорезь
Р = [τ’сp]·L·S ,
где,
[τ’сp] — допускаемое напряжение для сварного шва на срез.
СОЕДИНЕНИЕ ПРОБОЧНОЕ
Применяют в изделиях, не несущих силовых нагрузок. Пробочную сварку можно применять для соединения листов толщиной от 15 мм.
Если пробочные соединения подвергаются действию срезывающих сил, то напряжение
где,
d — диаметр пробки;
i — число пробок в соединении.
СОЕДИНЕНИЕ СТЫКОВОЕ
ПОД ДЕЙСТВИЕМ ИЗГИБАЮЩЕГО МОМЕНТА
При расчете прочности соединения (см. рис. 9), осуществленного стыковым швом, находящимся под действием изгибающего момента Ми и продольной силы Р, условие прочности
где,
W = Sh²/6;
F = hS.
При расчете прочности соединения (см. рис. 10, а), осуществленного угловым швом, находящимся под действием изгибающего момента Ми и продольной силы Р, расчетные касательные напряжения в шве
где,
Wc = 0,7Kh²/6;
Fc = 0,7Kh.
При расчете прочности соединений (см. рис. 10, б), состоящих из нескольких швов и работающих на изгиб, принимают (для приведенного графически случая), что изгибающий момент Ми уравновешивается парой сил в горизонтальных швах и моментом защемления вертикального шва
Если момент Ми и допускаемое напряжение τ заданы, то из полученного уравнения следует определить l и K, задавшись остальными геометрическими параметрами.
ДОПУСКАЕМЫЕ НАПРЯЖЕНИЯ ДЛЯ СВАРНЫХ ШВОВ
Допускаемые напряжения (табл. 1 и 2) для сварных швов принимают в зависимости:
а) от допускаемых напряжений, принятых для основного металла;
б) от характера действующих нагрузок.
В конструкциях из стали Ст5, подвергающихся воздействию переменных или знакопеременных нагрузок, допускаемые напряжения для основного металла понижают, умножая на коэффициент
где,
σmin и σmax — соответственно минимальное и максимальное напряжения, взятые каждое со своим знаком.
1. Допускаемые напряжения для сварных швов
в машиностроительных конструкциях при постоянной нагрузке
Сварка | Для стыковых соединений | При срезе [τ’ср] | |
при растяжении [σ’p] | при сжатии [σ’сж] | ||
Ручная электродами: Э42……….. Э42 А……. | 0,9[σp] [σp] | [σp] [σp] | 0,6[σp] 0,65[σp] |
[σp] — допускаемое напряжение при растяжении для основного металла. |
2. Допускаемые напряжения в МПа
для металлоконструкций промышленных сооружений
(подкрановые балки, стропильные фермы и т. п.)
Марка стали | Учитываемые нагрузки | |||||
основные | основные и дополнительные | |||||
вызывающие напряжения | ||||||
растяжения, сжатия, изгиба | среза | смятия (торцового) | растяжения, сжатия, изгиба | среза | смятия (торцового) | |
Подкрановые балки, стропильные фермы и т.п. | ||||||
Ст2 Ст3 | 140 160 | 90 100 | 210 240 | 160 180 | 100 110 | 240 270 |
Металлоконструкции типа крановых ферм | ||||||
Ст0 и Ст2 Ст3 и Ст4 Ст5 Низколеги- рованная | 120 140 175 210 | 95 110 140 170 | 180 210 260 315 | 145 170 210 250 | 115 135 170 200 | 220 255 315 376 |
Для конструкций из низкоуглеродистых сталей при действии переменных нагрузок рекомендуется принимать коэффициент понижения допускаемых напряжений в основном металле
где,
ν — характеристика цикла, ν = Рmin / Pmax; Рmin и Pmax соответственно наименьшая и наибольшая по абсолютной величине силы в рассматриваемом соединении, взятые каждая со своим знаком;
Ks — эффективный коэффициент концентрации напряжений (табл. 3).
3. Эффективный коэффициент концентрации напряжения Ks
Расчетное сечение основного металла | Кs |
Вдали от сварных швов | 1,00 |
В месте перехода к стыковому или лобовому шву (металл обработан наждачным кругом) | 1,00 |
В месте перехода к стыковому или лобовому шву (металл обработан строганием) | 1,10 |
В месте перехода к стыковому шву без механической обработки последнего | 1,40 |
В месте перехода к лобовому шву без обработки последнего, но с плавным переходом при ручной сварке | 2,00 |
В месте перехода к лобовому шву при наличии выпуклого валика и небольшого подреза | 3,00 |
В месте перехода к продольным (фланговым) швам у концов последних | 3,00 |
ПРИМЕРЫ РАСЧЕТА ПРОЧНОСТИ СВАРНЫХ СОЕДИНЕНИЙ
Пример 1. Определить длину швов, прикрепляющих уголок 100x100x10 мм к косынке
(рис. 11. а). Соединение конструируется равнопрочным целому элементу. Материал сталь Ст2. Электроды Э42.
В табл. 2 для стали Ст2 находим допускаемое напряжение [σp] = 140 МПа. Площадь профиля уголка 1920 мм² («Уголки стальные горячекатаные равнополочные» ГОСТ 8509-93).
Расчетная сила в уголке
Р = 140×1920 = 268 800 Н
В данном случае допускаемое напряжение при срезе, согласно табл. 1, в сварном шве
[τcp] = 140×0,6 = 84 МПа.
Требуемая длина швов (при К =10 мм) в нахлесточном соединении согласно расчету к рис. 11а.
Длина лобового шва l = 100 мм: требуемая длина обоих фланговых швов lфл = 458-100 = 358 мм. Так как для данного уголка е1 = 0,7l то длина шва 2 будет l2 — 0,7×358 = 250 мм, длина шва 1 будет l1 = 0,3×358 = 108 мм. Принимаем l2 = 270 мм, l1 = 130 мм.
Пример 2. Определить длину l швов, прикрепляющих швеллер №20а. нагруженный на конце моментом М = 2,4×107 Н·мм (рис. 11. б). Материал сталь Ст2. Электроды Э42.
В табл. 2 для стали Ст2 находим допускаемое напряжение [σp] = 140 МПа. Допускаемое напряжение при срезе, согласно табл. 1, в сварном шве
[τ’cp] = 140×0,6 = 84 МПа.
Момент сопротивления сечения швеллера W = 1,67 x 105 мм³ (из ГОСТа)
Напряжение
σ = 2,4×107 / 1,67×105 = 144 МПа
Катет горизонтальных швов К1 = 10 мм, вертикального К2 = 7,5 мм. Из формулы 1 (см. выше) находим
Принимаем l = 200 мм. При этой длине шва напряжение при изгибе
Полученная величина меньше допускаемой [τ’cp] = 84 МПа.
ЭЛЕКТРОДЫ
Размеры и общие технические требования на покрытые металлические электроды
для ручной дуговой сварки сталей и наплавки поверхностных слоев из сталей и сплавов приведены в ГОСТ 9466-75 или кратко здесь.
Электроды покрытые металлические для ручной дуговой сварки
конструкционных и теплоустойчивых сталей (по ГОСТ 9467-75):
Электроды изготовляют следующих типов:
Э38, Э42, Э46 и Э50 — для сварки низкоуглеродистых и низколегированных
конструкционных сталей с временным сопротивлением разрыву до 500 МПа:
Э42А, Э46А и Э50А — для сварки углеродистых и низколегированных конструкционных сталей с временным сопротивлением разрыву до 500 МПа, когда к металлу сварных швов предъявляют повышенные требования по пластичности и ударной вязкости;
Э55 и Э60 — для сварки углеродистых и низколегированных конструкционных
сталей с временным сопротивлением разрыву св. 500 до 600 МПа;
Э70, Э85, Э100, Э125, Э150 — для сварки легированных конструкционных сталей
повышенной и высокой прочности с временным сопротивлением разрыву свыше 600 МПа;
Э-09М, Э-09МХ, Э-09Х1М, Э-05Х2М, Э-09Х2МГ, Э-09Х1МФ, Э-10Х1М1НФБ, Э-10ХЗМ1БФ, Э-10Х5МФ — для сварки легированных теплоустойчивых сталей.
Механические свойства металла шва,
наплавленного металла и сварного соединения при нормальной температуре (по ГОСТ 9467-75)
Типы электродов | Металл шва или наплавленный металл | Сварное соединение, выполненное электродами диаметром менее 3 мм | |||
Временное сопротивление разрыву σв, МПа (кгс/мм²) | Относительное удлинение δ5, % | Ударная вязкость KCU, Дж/см² (кгс·м/см²) | Временное сопротивление разрыву σв, МПа (кгс/мм²) | Угол загиба, градусы | |
не менее | |||||
Э38 | 380 (38) | 14 | 28 (3) | 380 (38) | 60 |
Э42 | 420 (42) | 18 | 78 (8) | 420 (42) | 150 |
Э46 | 460 (46) | 18 | 78 (8) | 460(46) | 150 |
Э50 | 500 (50) | 16 | 69 (7) | 500 (50) | 120 |
Э42А | 420 (42) | 22 | 148 (15) | 420 (42) | 180 |
Э46А | 460 (46) | 22 | 138 (14) | 460 (46) | 180 |
Э50А | 500 (50) | 20 | 129 (13) | 500 (50) | 150 |
Э55 | 550 (55) | 20 | 118 (12) | 550 (55) | 150 |
Э60 | 600 (60) | 18 | 98 (10) | 600 (60) | 120 |
Э70 | 700 (70) | 14 | 59 (6) | — | — |
Э85 | 850 (85) | 12 | 49 (5) | — | — |
Э100 | 1000 (100) | 10 | 49 (5) | — | — |
Э125 | 1250 (125) | 8 | 38 (4) | — | — |
Э150 | 1500 (150) | 6 | 38 (4) | — | — |
ГОСТ 9467-75 предусматривает также типы электродов и механические свойства наплавленного металла или металла шва для легированных теплоустойчивых сталей.
Электроды покрытые металлические для ручной дуговой наплавки
поверхностных слоев с особыми свойствами (по ГОСТ 10051-75)
Тип | Марка | Твердость без термообработки после наплавки HRC | Область применения |
Э-10Г2 Э-11Г3 Э-12Г4 Э-15Г5 Э-30Г2ХМ | ОЗН-250У O3H-300У ОЗН-350У ОЗН-400У НР-70 | 22,0-30,0 29,5-37,0 36,5-42,0 41,5-45,5 32,5-42,5 | Наплавка деталей, работающих в условиях интенсивных ударных нагрузок (осей, валов автосцепок, железнодорожных крестовин, рельсов и др.) |
Э-65Х11Н3 Э-65Х25Г13Н3 | ОМГ-Н ЦНИИН-4 | 27,0-35,0 25,0-37,0 | Наплавка изношенных деталей из высокомарганцовистых сталей типов Г13 Г13Л |
Э-95Х7Г5С Э-30Х5В2Г2СМ | 12АН/ЛИВТ ТКЗ-Н | 27,0-34,0 51,0-61,0 | Наплавка деталей, работающих в условиях интенсивных ударных нагрузок с абразивным изнашиванием |
Э-80Х4С Э-320Х23С2ГТР Э-320Х25С2ГР Э-350Х26Г2Р2СТ | 13КН/ЛИВТ Т-620 Т-590 Х-5 | 57,0-63,0 56,0-63,0 58,0-64,0 59,0-64,0 | Наплавка деталей, работающих в условиях преимущественно абразивного изнашивания |
Э-300Х28Н4С4 Э-225Х10Г10С Э-110Х14В13Ф2 Э-175Б8Х6СТ | ЦС-1 ЦН-11 ВСН-6 ЦН-16 | 49,0-55,5 41,5-51,5 51,0-56,5 53,0-58,5 | Наплавка деталей, работающих в условиях интенсивного абразивного изнашивания ударными нагрузками |
ГОСТ предусматривает также и другие химический состав, типы и марки электродов.
Сварочные материалы, применяемые для сварки стальных конструкций, должны обеспечивать механические свойства металла шва и сварного соединения (предел прочности, предел текучести, относительное удлинение, угол загиба, ударную вязкость) не менее нижнего предела свойств основного металла конструкции.
Свариваемые материалы и применяемые электроды:
— СтЗкп, СтЗкп, СтЗпс, Сталь 08кп, Сталь 10 — Э42, Э42А, Э46;
— Сталь 20 — Э42;
— Сталь 25Л — Э46;
— Сталь 35Л, Сталь 35, Сталь 45, Ст5кп, Ст5пс — Э50А;
— Сталь 20Х, Сталь 40X — Э85;
— Сталь 18ХГТ, Сталь 30ХГСА — Э100;
— АД1, АД1М, АМг6 — Присадочные прутки.
Подробную классификацию покрытых электродов и область применения смотри здесь.
Источник
Прочность сварных соединений — это возможность в определенных условиях выдерживать нагрузки, не разрушаясь от силовых воздействий. Нагрузки при этом учитываются не только рабочие, но и предельные.
Рабочие состоят из внешних нагрузок, возникающих в процессе эксплуатации от собственного веса и образующихся при сваривании напряжений. К предельным относят те, которые образуются при текучести в основном сечении и в при этом возникают максимально допустимые деформации и повреждения. Чтобы стыки были надежными и качественными, то перед процессом сваривания необходимо выполнить расчет на прочность сварного шва.
От чего зависит прочность сварочного стыка
Чтобы правильно вычислить прочность сварного шва, необходимо знать какие факторы влияют на прочностные характеристики. Главное условие для создания прочных соединений — соблюдение сварочной технологии.
Но есть также ряд других факторов, от которых зависит насколько качественным будут стыки:
- качество используемых материалов. Коэффициент прочности сварного шва напрямую зависит от того, насколько правильно подобран окружающий металл и какими характеристиками он обладает;
- расходные материалы. Неверно подобранные присадки или электроды не способны сформировать надежное соединение;
- сварочное оборудование должно отвечать требуемой мощности и технологии сварки;
- надежность и качество провара зависит от режима сварки, в частности от силы тока и полярности;
- качество заготовок. На кромочных стыках не должно быть никаких изъянов и вкраплений, поскольку это нарушает форму и прочность шва.
Каждый из этих параметров должен учитываться при планировании сварочных работ и от каждого из них зависит насколько точно будет произведен расчет на прочность сварных соединений.
Как рассчитать на прочность сварочные швы
В зависимости от того, как размещены при сваривании соединяющие элементы, выделяют разные типы швов: угловые, стыковые, тавровые, нахлесточные. На фото ниже можно посмотреть разные способы соединения между собой свариваемых деталей.
Для каждого вида соединений расчет сварных швов на прочность проводится индивидуально и с учетом разных параметров. Прочностные значения стыковых швов определяются по номинальному сечению проваренного участка, на котором отсутствуют наплывы. Для угловых соединений прочностные показатели определяет катет.
В любом случае прежде чем осуществлять расчет прочности сварного шва, необходимо вычислить площадь его поперечного сечения. Установить сечение можно при умножении длины и толщины сварочного соединения.
Определить допускаемое усилие в стыке при растяжении можно по формуле: Р = σp × S × I
При сжатии формула несколько другая: Р = σсж × S × I
Условные обозначения в формулах следующие:
- S — толщина элементов, которые соединяются техникой сваривания;
- I — длина сварочного соединения;
- σp — допустимое напряжение при растяжении;
- σсж — допустимое напряжение при сжатии.
Вычислить какой прочностью будет обладать нахлесточный шов можно по формуле: Р = τср × 0,7К × I, в которой:
- Р — допустимо возможное усилие;
- τср — показатель допускаемого напряжения металла, наплавленного при срезе;
- К — длина катета, которая в формуле проставляется с коэффициентом 0,7;
- I — протяжность соединительного стыка.
Вычисляя несущие возможности стыкового шва необходимо ориентироваться на напряжение, которое является допустимым в самом опасном сечении (s), а также на напряжение, зависящее от предела текучести (HSЭ). Выдерживание соотношений этих двух показателей является обязательным и только при полном их соответствии элемент металлоконструкции будет удовлетворять все выдвигаемые к прочностным характеристикам требования.
Основная задача при подготовке к свариванию металлоконструкций — не превысить максимально допускаемые напряжения рассчитывая прочность сварного шва на разрыв, таблица коэффициентов которого есть на специализированных сайтах в интернете в свободном доступе.
Онлайн расчет прочности стыков
Проведение предварительных расчетов прочности перед свариванием металлоизделий позволяет предотвратить неточности и браки, приводящие к разрушению конструкций. Чтобы безошибочно провести расчет сварных швов на прочность примеры готовых вычислений могут послужить в качестве инструкций правильности выполнения всех действий. А исчислять прочностные свойства лучше всего в онлайн режиме, воспользовавшись специальными программами «Калькулятор прочности».
С помощью программы не составить сложности без погрешностей вычислить несущую способность швов по длине и катету, подобрать диаметр арматуры согласно требуемой на разрыв нагрузки, установить площадь поперечного сечения и рассчитать другие значения, от которых зависит прочность и надежность сварных конструкций.
Интересное видео
Источник